Improve sustainability via enhanced maintenance
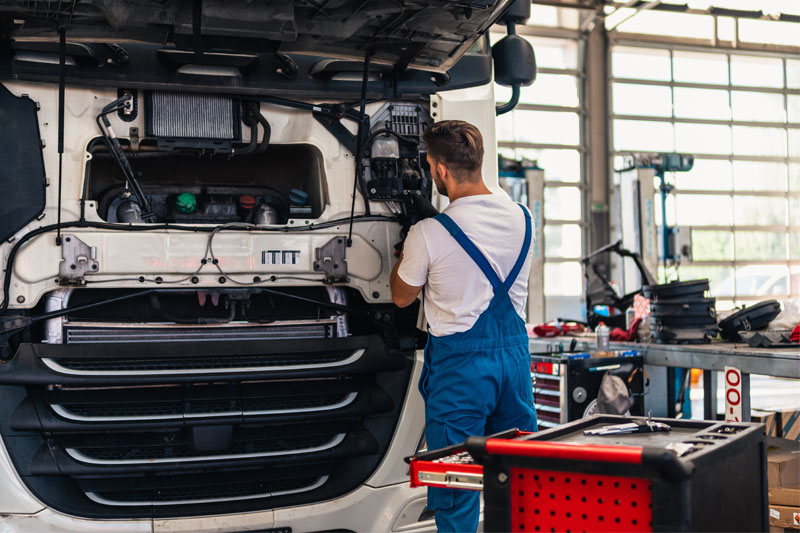
In an era where fleet managers grapple with the choice between electric and internal combustion vehicles, enhanced maintenance emerges as a strategic third path, argues Paul Dobbyn, director, Powerflow Ltd.
Fleet managers are currently navigating a challenging decision-making landscape, pondering whether to adopt electric vehicles (EVs) or buy new internal combustion engine (ICE) vehicles. The consensus advice seems to lean towards patience.
The introduction of EVs poses logistical hurdles, including concerns about range and recharge times, while acquiring new ICE vehicles is hindered by long lead times and the dual concerns of initial expense and potentially poor residual values.
There is a third way, though. Enhanced maintenance, a regime that goes beyond the recommendations of the manufacturer, can deliver a vehicle that lasts longer and operates more efficiently and that also promotes the overall aim of sustainability by doing so.
ICE challenges
If you can keep your current ICE vehicle then you lower your capital costs because you do not need to raise a massive deposit and pay the purchase costs. You also have a far lower carbon footprint. Whether it is an EV or and ICE any new vehicle will involve emitting tonnes of CO2 during manufacture, while an EV requires tonnes of CO2 just to mine the precious metals needed for its battery. According to the International Energy Agency, electric cars use 173kg more minerals such as lithium, nickel and copper than petrol cars. Now, extrapolate that to a commercial vehicle.
Nevertheless, the decision to keep ICE vehicles operational is not without its challenges, notably the potential for increased maintenance expenses and the risk of more frequent operational downtime. But these concerns can be effectively managed and mitigated through a robust enhanced maintenance programme. Enhanced maintenance is not merely an upgrade to standard practices but a necessary evolution for those seeking to extend the operational lifespan of their vehicles beyond the typical three-year tenure.
Large fleet operators have already recognised that clean engines perform more efficiently and have a direct impact on the longevity of the vehicle. This maintenance strategy focuses on the deep cleaning of engine components to remove soot and other by-products of combustion, which if left unchecked, contribute to the wear and tear of engine parts.
Soot reduction
Soot is both a side effect and a cause of wear in engine components. Soot is carbon, one of the hardest known substances. When soot meets oil it has a has a tendency to connect to other soot particles to make bigger soot particles. The result is like having a liquid emery paper flowing around the engine.
The soot is the inevitable by-product of combustion so you cannot stop it occurring. Yet it can be reduced dramatically – and this is vital to keeping an engine working and working efficiently.
Case Study
Service: BG 109 Compression Performance Restoration
Products: BG 109, PN 10932, one quart (946 ml), BG SAE 15W-40 Synthetic Blend Engine Oil, PN 714
Vehicle: 2008 Ford F-250, Power Stroke® 6.4L
Mileage: 4,859 miles (72,194 km)
Maintenance history: Regular oil changes performed
Driving conditions: Avg. 35 miles (56 km) per day city
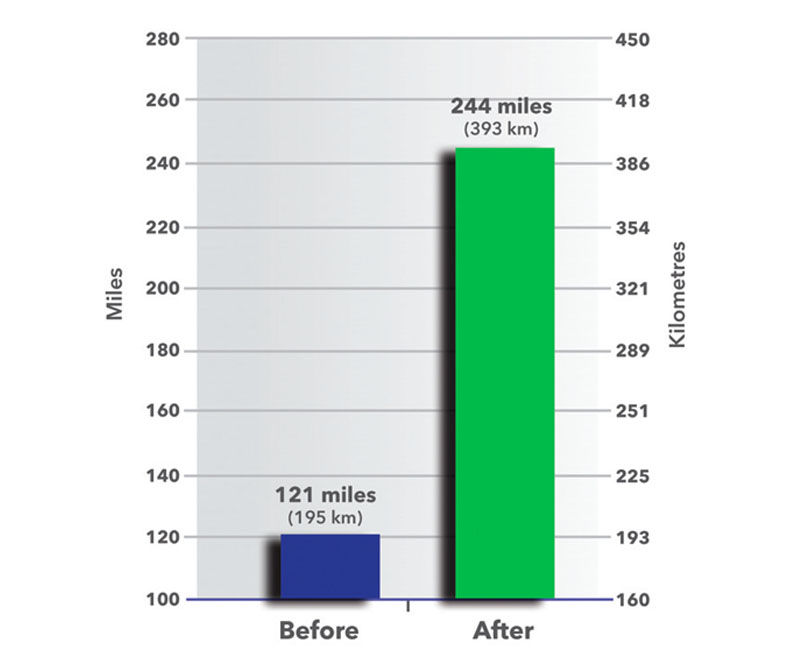
(miles/km driven between regeneration cycles)
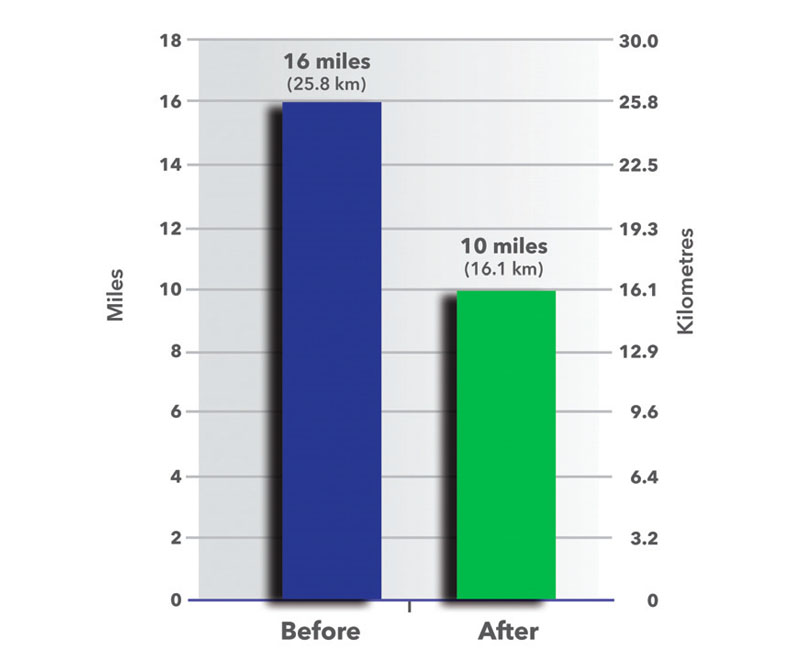
(miles/km driven between regeneration cycles)
Soot will deposit itself very quickly on several key components, most damagingly the fuel injectors and the piston rings.
When soot attaches to or inside an injector this interferes with the atomisation of the injector causing inefficient combustion and, as a result, yet more soot. When soot and degraded oil get behind the piston rings it restricts the rings ability to flex and centre. This means that the seal is compromised and leads, very quickly, to two other effects: lost compression and more oil combustion.
Three elements of success
Lost compression also means compromised combustion and consequently more soot – and so the vicious circle carries on. An under-appreciated but actually a major cause of diesel particulate filter (DPF) decline is the impact of oil seeping past the rings, combusting and then depositing metals such as zinc, calcium, magnesium and others onto the DPF – even with low SAPS (sulphated ash, phosphorus, and sulphur) oils. These metal elements effect the efficiency, and shorten the life, of the DPF. DPF life is extended when combustion is optimised. Restoring compression means less soot is produced and the DPF is required to do less regenerations.
Deposits on injectors form relatively quickly in a modern engine and the effect is compounded by the much tighter specifications of an injector, with its ever decreasing aperture size. Deposits in, or on, the injector interfere with the spray atomisation making it harder for optimum combustion. This leaves even more deposits, poor fuel consumption and fuel dilution of the oil – which has its own knock-on effects on the oil’s ability to lubricate effectively.
All this is both known and accepted as a real and present problem by fleet managers, yet so many fleet managers stick to the OEM schedule, which does not mention injector and other engine cleaning measures. This is despite their own fuel charter stating that keeping injectors clean is a priority if they want to maintain the specified performance, fuel consumption and emissions.
The whole notion of enhanced maintenance boils down to just three elements:
- service interval injector and fuel system cleaning to restore accurate fuel delivery
- engine cleaning (pre-oil change) to free piston rings, restore compression, reduce blow-by
- oil supplementation to help control soot agglomeration, control acid formation and to maintain viscosity for longer.
By adhering to a regimen that exceeds standard maintenance protocols, fleet managers can significantly reduce the accumulation of soot and other contaminants within the engine. This approach involves a comprehensive cleaning of fuel injectors and piston rings, areas particularly susceptible to soot accumulation.
Proactive approach
The benefits of such maintenance include restored engine compression, optimised fuel combustion, and extended diesel particulate filter (DPF) life by minimising the need for regeneration cycles.
Furthermore, enhanced maintenance includes the use of fuel system cleaners and engine performance restoration products, as well as oil enhancers that work to maintain oil viscosity and prevent the negative effects of soot aggregation.
This proactive maintenance does not require additional labour time, as it integrates seamlessly with scheduled service intervals, making it a cost-effective solution for extending vehicle life, enhancing performance, and maintaining fuel efficiency.
In summary, enhanced maintenance represents a strategic pivot from the conventional wisdom of fleet renewal through the acquisition of new vehicles, be they EV or ICE. By focusing on the meticulous care and upkeep of existing fleets, fleet managers can achieve operational efficiency, environmental responsibility, and financial prudence, all while preparing for the future of transportation.