Maintaining clear windscreen visibility
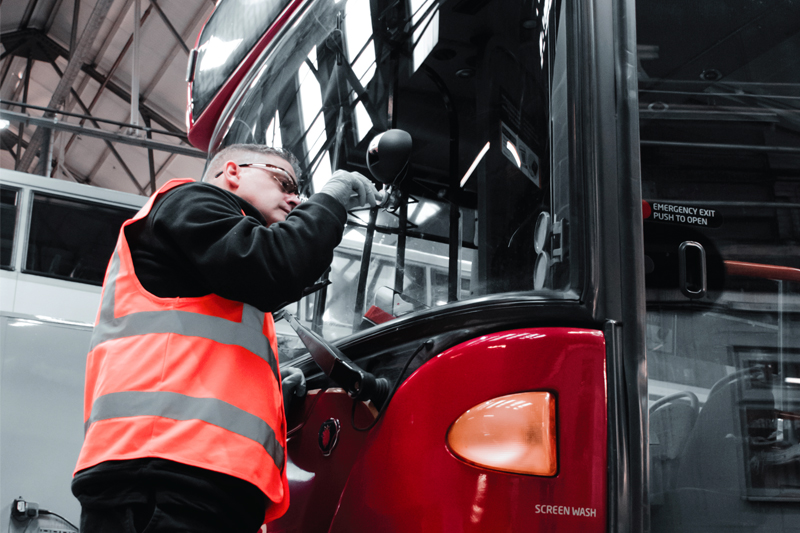
When running a fleet of vehicles, safety is obviously a key consideration, and maintaining perfect visibility from windscreens is vital. Dean Proctor, head of training and technical at Esprit Windscreen Repair Equipment, elaborates.
If a screen has a chip, it can turn easily into a crack, and can possibly leave the vehicle off the road until the screen can be replaced, and all at additional cost to operators. For drivers, a screen without imperfections means visibility through the glass is (subject to cleaning) perfect and their vision isn’t obscured, nor are they distracted by marks on the screen.
And thanks to modern proprietary windscreen systems, many fleet companies are now largely able to repair their own screens in-house. This is quite straightforward and necessarily saves time, money and reduces vehicle downtime.
Rather than entrust screens to any repair system, it pays to choose an established one – for instance, so Esprit was developed over 40 years ago – and one with a focus on large screens, especially those increasingly being used from the 1980s onwards.
Inject, cure, ready
The system has certainly improved since then (it used to take an afternoon to cure the resin, now it takes 75 seconds!) but at the heart of it, the principles remain the same: resin is injected into a break, cured and the screen is ready.
Unfortunately, in 2000, the British Standards committee moved away from performance-based criteria for assessing windscreen repair systems: a poor decision in our opinion. Consequently, in the absence of a meaningful BS to rely on, buyers should look for other, credible accreditations. One such independent test comes from TUV Rheinland, a performance product test that ensures repairs are up to the same standard as a new screen (the ECE R43 test). But what if staff have never carried out windscreen repair before? Is it straightforward?
Actually, it is simple to learn and the leading companies, like Esprit, carry out in person training. In our case, which could be at our Staffs HQ (free) or onsite (for a fee). This could be for a whole team, and as a refresher course if needed.