What’s changing in DVSA brake testing?
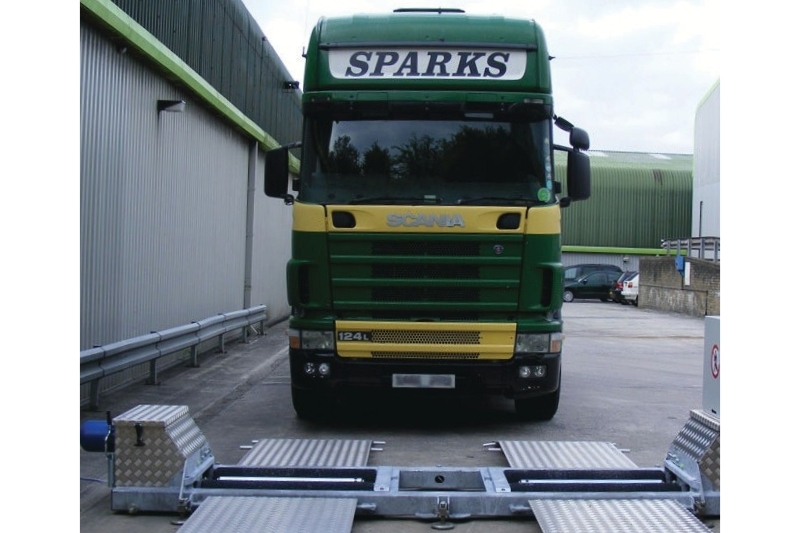
Mike Walker of Liftmaster looks at the importance of ATFs understanding updated DVSA brake testing regulations, and, in particular, what it means for roller brake testers.
The Driver and Vehicle Standards Agency (DVSA) has introduced updated regulations for brake testing procedures for Heavy Goods Vehicles (HGVs) and Public Service Vehicles (PSVs). These changes aim to standardise testing practices across the industry, enhancing road safety and ensuring more accurate assessments.
The implementation of these changes began in June 2024, where all new roller brake testers (RBT) sold from that point had to be updated with the new software enhancements, with further changes taking place over the course of this year.
For ATFs, this offers both challenges, such as equipment upgrades and training, but also new opportunities to offer safer, more efficient services.
What are the changes?
In short, they are the following:
- Laden roller brake tests (RBTs): vehicles are tested on rollers while carrying a load that meets the required weight criteria (at least 65% but no less than 50% of the axle design weight).
- Electronic brake performance monitoring systems (EBPMS): for vehicles unable to be physically loaded, EBPMS can monitor brake performance electronically.
- Software updates for roller brake testers: featuring improved workflows, on-screen warnings, enhanced printouts, RAG system, simplified brake reports and instructions for advanced testing.
When?
Some of the changes have already taken place, with all new roller brake testers purchased after June 2024 being sold with the new software updates. Any RBTs purchased prior to this date will require their software to be updated by December 2025. However, it’s worth bearing in mind that some older RBTs may not be compatible with the new software and will therefore require a complete upgrade of the RBT with the new software pre-installed.
Laden testing will become mandatory from April 2025. ATFs must ensure that by this point they have the ability to either test under real-world conditions, with a physical load (at least 65% but not less than 50% of the axle design weight) or have electronic brake performance monitoring systems (EBPMS) in place for vehicles unable to carry a load during testing.
Why?
The primary objective is to improve road safety by ensuring that brake performance assessments reflect real-world operating conditions – with a more detailed understanding of any faults. By measuring brakes under load conditions, it provides a more accurate measure of their effectiveness, thereby reducing the risk of brake-related incidents. Furthermore, standardising brake testing procedures across the industry aims to:
- enhance consistency: uniform testing methods lead to more reliable maintenance practices.
- ensure compliance: clear guidelines help workshops adhere to legal requirements, minimising the risk of non-compliance penalties.
- promote best practices: encouraging the use of advanced testing methods fosters a culture of safety and diligence within the industry.
Your workshop
While these changes may pose challenges, they are essential for maintaining compliance and ensuring safety. Workshops that fail to meet the deadlines run the risk of losing compliance and, therefore, potential closure. It is vital that workshops understand the changes and what action needs to be taken in order to remain compliant.
First off, we’d recommend auditing current RBTs to identify any compliance gaps as early as possible. Manufacturers will see a significant increase in demand, and therefore, leaving these upgrades close to the deadline may mean that there’s a delay for the upgrades to commence, resulting in downtime and disrupting operations.
ATFs that get ahead of the curve, ensuring they are compliant and meet the DVSA regulations early on, will minimise the impact on their operations. For any advice, contact the Liftmaster team where a representative will be happy to assist with any questions you may have.
The best preparation
Doing nothing is not an option, so the best way forward is to gain an understanding of the new requirements as soon as possible. Familiarise yourself with the updated Guide to Maintaining Roadworthiness, which outlines the new brake testing expectations and provides detailed guidance on conducting laden brake assessments.
Then assess your current equipment and procedures. You should evaluate your testing equipment and determine if your current roller brake testers can accommodate laden testing, if upgrades are necessary, and if your current RBT can support the new software.
Follow that by reviewing testing procedures, so that you ensure that your current safety inspection processes can incorporate laden brake tests or EBPMS assessments as required.
It goes without saying that you will need to implement any necessary upgrades. If your current equipment does not meet the new specifications, plan for necessary upgrades or replacements. Provide training for technicians to effectively use new equipment and understand the updated testing procedures.
If in any doubt the best course of action is to seek out expert advice. Speak to equipment suppliers to understand the capabilities of new testing devices and receive guidance on the best solutions for your workshop’s needs – earlier rather than later!
And just as a reminder the key dates are April 2025 when laden testing becomes mandatory and then December 2025 when all roller brake testers must be updated with the new software.
Our advice is don’t wait until the last minute! You can always contact us at Liftmaster and speak to one of our experts who will be happy to help!