How to fault find a fuel pressure issue
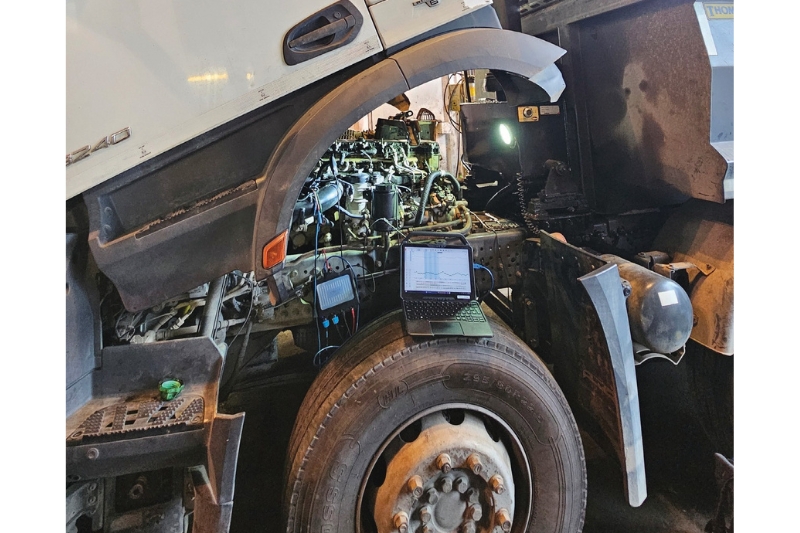
Ben Martins, automotive application specialist from Pico Technology, gets to the bottom of a fuel pressure fault on a 2017 Mercedes Arocs truck.
One thing I love about this industry is that there is always something new to learn. Despite experience, surprises still arise! This was the case with a 2017 Mercedes Arocs truck (309,114km) showing a fuel pressure fault. The warning lights appeared, followed by limp mode. The issue had persisted for three months, difficult to diagnose due to its intermittency. As the fault worsened, it became easier to replicate and pinpoint.
The main fault codes were:
- A4000F – High-pressure fuel circuit not OK.
- 9D000A – Upper-level limit for rail pressure regulation reached.
Freeze frame data showed a 200-bar difference between desired and actual pressure, but no low-pressure supply issue when the fault was set.
Previous repairs
The truck had been in and out of the workshop for various issues. Parts replaced included:
- Rail pressure sensor reading 13 bar with the engine off.
- Inlet metering valve stuck, causing erratic idle. A new high-pressure pump resolved this.
- Injectors 1 and 6 flagged by a high-pressure test and replaced.
After these replacements, the fault persisted.
Identifying the noise
A squeak was noticed at high idle from the high-pressure injector common rail, coinciding with rail pressure fluctuations. When deviation exceeded limits, fault codes were triggered.
To investigate, we tapped into the spill return from the cylinder head and added a sight block. This allowed us to measure pressure and observe fuel flow for air bubbles, a potential culprit. We also used an accelerometer from the NVH kit to capture noise data.
By attaching the accelerometer to injector pipes, we saw high-frequency noise on cylinders 1, 3 and 4. The fuel rail pressure sensor also showed erratic behaviour. With this insight, we included the spill return pressure while monitoring fuel flow.
Understanding the waveform
Modern vehicle fuelling issues aren’t always straightforward due to ECU compensation for poor-performing cylinders. Analysing waveforms, we noted irregularities in the spill return for cylinders 2, 3, 4, and possibly 6. Two possibilities emerged:
- Bigger pulse: higher flow, possibly a failing injector.
- Smaller pulse: over-fuelling injector.
Finding the cause
The sight block revealed a significant amount of air in the return. Were the bubbles related to the squeak? To test this, we restricted the return line pressure using a stop tap while monitoring with the WPS500X sensor. When pressure increased, the noise stopped, and rail pressure stabilised. Key observations:
- Noise coincided with bubbles in the return.
- Rail pressure fluctuated when bubbles were present.
- Return line pressure was 0.5 bar when noise occurred.
- Raising return pressure to 1 bar stopped the noise and stabilized rail pressure.
Given this, air likely entered from the high-pressure side. With the pump already replaced, possibilities included a porous cylinder head or failing injector sleeves.
Confirming the fault
A call to a specialist confirmed that a failed injector sleeve could allow cylinder air to enter the fuel return gallery. During compression, this air could disrupt injector operation, cause noise, and introduce bubbles into the return.
To pinpoint the faulty injector(s), we opted to replace all six sleeves while the cooling system was drained. Upon inspection, injector 4 stood out.
The key discovery
Injector 4 displayed discoloration, but the real issue appeared when removing the sealing washer – a crack in the injector body. This crack may have contributed to return pressure inconsistencies.
With injector 4 and all six sleeves replaced, the truck was reassembled. The cooling and fuel systems were bled, and testing resumed.
Post-repair results
Rail pressure and fuel return pressure data showed significant improvements:
- Rail pressure stabilized (now green on the graph).
- Return pressure remained steady at 1 bar.
- Defined pulses in the return line, aligning with injector spill events.
- No more air bubbles in the return.
Interestingly, prior captures suggested cylinder 4 as the issue. Reviewing accelerometer data in spectrum mode further highlighted injector 4’s anomaly.
Deeper analysis with PicoScope 7
Using PicoScope 7 Automotive for waveform analysis provided a more in-depth understanding of injector behaviour. The software allowed us to isolate individual injector waveforms and analyse high-frequency anomalies more clearly. When switching to spectrum mode, it became evident that injector 4 exhibited unique characteristics compared to the others. This non-intrusive testing method is invaluable for diagnosing similar faults in the future, reducing the need for unnecessary part replacements.
Lessons learned
This case highlights the importance of using advanced diagnostic tools and methodologies rather than relying solely on traditional mechanical assessments. A combination of NVH analysis, sight block testing, and waveform examination proved instrumental in diagnosing the root cause.
Thanks to Lee Sharp at L&D Commercials Ltd for the opportunity to work on this case!