How to stay compliant
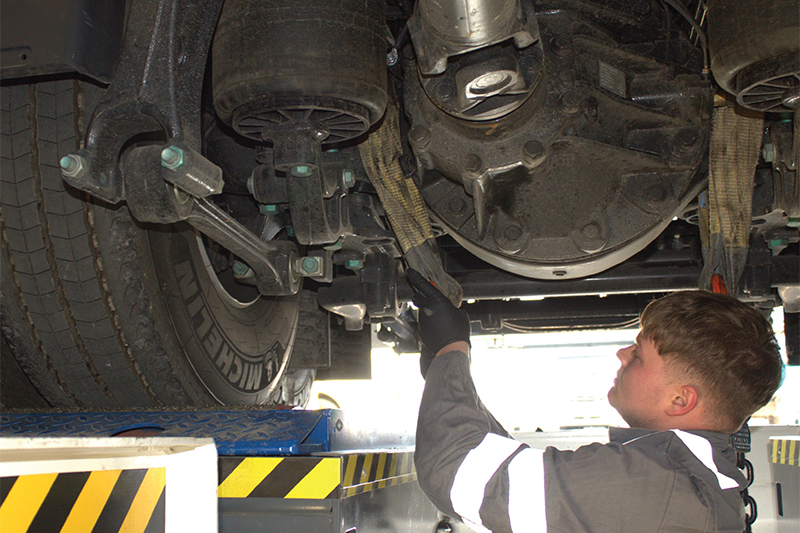
MAHA UK, Manchetts and Premier Pits collaborated on new ATF lane for Manchetts Group’s Sleaford depot – featuring a rising roller brake tester.
According to the DVSA’s guide to maintaining roadworthiness: commercial goods and passenger carrying vehicles, it is expected that every safety inspection will include a brake performance assessment using either a roller brake test, a suitable electronic braking performance monitoring system (EBPMS) or a decelerometer with temperature readings.
In the guidance, DVSA states that conducting a laden brake test using a calibrated roller brake tester is the “most effective method of measuring individual and overall braking performances”.
MAHA UK’s MBT 7250 commercial brake tester includes a rising roller bed option. It can be raised by 250mm; doing so simulates axle loads of up to 10 tonnes and offers a reliable alternative to traditional laden testing when external loading isn’t possible.
Space constraints, time inefficiency, availability of load equipment, safety risks, operational restrictions and vehicle suitability are all possible reasons for this – but, nevertheless, staying compliant with the latest legislation is paramount.
At Manchetts Group’s Sleaford depot, it has taken a major step forward towards this goal with the installation of a new ATF lane. Delivered in partnership with MAHA UK and Premier Pits, the project has highlighted the importance of collaboration, namely teamwork, leadership and speed.
Manchetts is a family-run business and a Cambridgeshire top 100 company, specialising in HGV and LCV vehicle service, repair and roadside recovery. Beginning as a single site, the company matured and stretched its presence across Cambridgeshire, Suffolk and Lincolnshire – the acquisition of new HGV workshops, previously MAN Sleaford, its latest strategic acquisition.
This was a significant milestone and boost to Manchetts’ business plan of expanding along the A1 corridor – complementing the purchase of its award-winning Peterborough site in 2020.
Manchetts business development manager, Lindsay Powell, explained why the installation of a new ATF lane was a vital investment: “As a business, we are always looking to create the perfect partnership with our customers. The ATF lane and rising brake rollers were essential at our Sleaford depot to make sure that we have a one-stop-shop for our customers, new and existing.”
Branch manager, Aaron Woods, concurred – adding that the need for an ATF lane became clear as the demand for brake testing and vehicle inspections increased: “We’ve undergone a lot of changes since opening in February 2024,” he said. “We needed to cater for both our regular MAN customers and growing multi-brand inspection requirements. This included meeting new DVSA standards on meaningful brake testing.”
MAN Sleaford was no stranger to MAHA UK; prior to Manchetts assuming control of the site, there was a 17-year-old MAHA brake tester installed. Bullishly, Aaron revealed the IW7 had “never let us down” and was “bulletproof”. He added: “The backup from MAHA UK has always been brilliant too.” This was echoed by Lindsay:
“MAHA’s equipment is proven, high quality and stands the test of time,” she said, “so we didn’t hesitate in proceeding with MAHA with this latest project.”
Technical challenge
This project had to be undertaken without disrupting Manchetts’ day-to-day environment, a challenge that required “careful coordination, clear zoning and experienced contractors”, according to MAHA UK’s workshop equipment specialist, Louis Tunmore. That is where Premier Pits came in; with 35 years’ experience in designing, manufacturing and installing prefabricated vehicle pits to partners globally, Manchetts was in safe hands.
The installation team and workshop staff worked harmoniously, enabling the smooth installation of a DVSA-spec ATF pit, one that was deeper than normal and with strict entry and exit specifications. Premier Pits marketing manager, Matt Dilley, explained how this particular part of the process unfolded: “We know that local conditions, especially in Lincolnshire where unstable ground can cause cave-ins, can be problematic, but our team managed the dig and installation without delays.
“Communication with MAHA UK and Manchetts was key – once the pit is in, it’s in for good. Precision matters.”
Made for the future
At the heart of the lane, of course, is the MBT 7250 braker tester with the hydraulic rising roller bed option. As mentioned, unlike traditional systems that use a trailer or loading weights, this technology simulates axle load by lifting it.
Louis dived into the technology: “This generation lifts the axle rather than pulling it down. There’s a restraint system in place to keep the vehicle stable during the test, ensuring the added weight is pushed into the axle rather than lifting the whole truck. This complies with DVSA requirements for a meaningful brake test – 65 per cent of gross axle weight must be replicated.”
The result? Aaron revealed that this method was “quicker and safer than loading the trailer with weights and much easier to operate”. He added: “Our technicians, both seasoned and newly qualified, have adapted quickly and collaboratively to the new equipment.”
Safety, compliance and DVSA collaboration
Safety and regulatory compliance were critical from day one. The DVSA was involved in the planning phase, offering input to avoid issues that could delay final approval. CCTV coverage, pit safety interlocks and minimum spacing regulations were all part of the design and walk-through inspections.
“The DVSA has hard-and-fast rules for ATF lanes,” Louis explained. “It is vital that their operatives are safe. That means no trip hazards, no unnecessary obstructions and no delays. With Premier Pits and MAHA both working closely with DVSA and the Garage Equipment Association (GEA), the lane met the requirements.”
An informal DVSA site visit ahead of the official sign-off gave Manchetts a head start – Lindsay said: “A few minor tweaks were needed, but that’s the benefit of working with experienced suppliers.”
Building for the future
The lane includes, not just the rising roller brake tester, but also axle play detectors, headlight alignment tester and radius plates to support Class 7 vehicles – everything needed for a full ATF lane. All of this equipment was installed within the existing workshop building, meaning no structural extensions.
“The finished pit is bright, safe and functional,” said Matt. “It’s a textbook installation!”
Staffing has also been a priority at the Sleaford site, ensuring the right balance between experienced professionals and new talent: “We have 14 technicians and 5 support staff,” said Aaron. “We also have apprentices and recently qualified staff who bring energy and a willingness to learn. It’s a great blend when introducing new technology, like the rising roller brake tester.”
What’s next?
With DVSA final sign-off imminent, Manchetts is already looking ahead: “We’ve had the DVSA here for the last checks, and we’re hopeful that we can announce our ATF lane opening very soon,” Lindsay said optimistically.
“Having this facility in place will mean quicker turnaround times for customers and full control over compliance.”
For Louis, the Sleaford project is a blueprint for how to do the job right: “Any partner we work with has to know garage equipment inside out. We don’t just use local builders; we use professionals, like Premier Pits, because our reputation and our clients’ compliance depend on it.”
Ultimately, this is a case study – a great example – in what happens when experience, professionalism and teamwork come together.