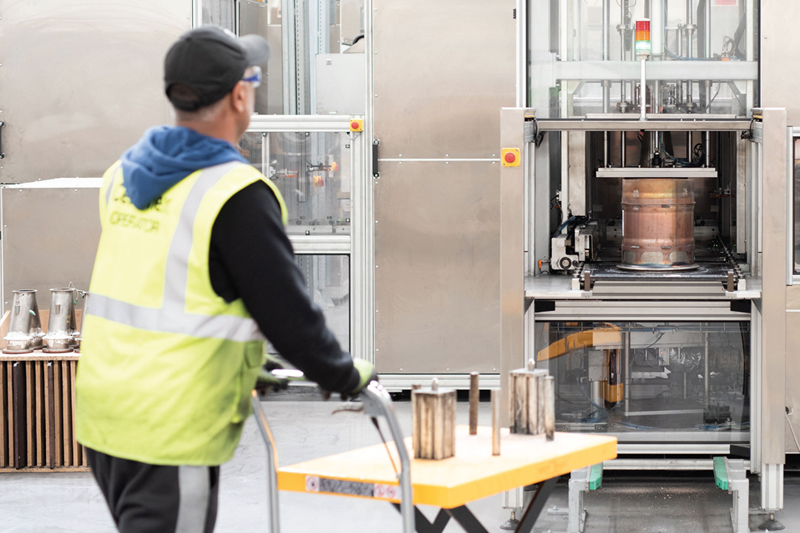
Barney Milles, managing director of Ceramex, explains the benefits of and process behind the company’s HGV DPF remanufacturing.
Remanufacturing is a fundamental part of a more sustainable ‘circular economy,’ where raw materials are conserved and energy consumption and landfill waste are reduced. Whilst traditional automotive remanufacturing has focused on returning items such as engines, transmissions and electrical components to ‘as new’ condition, demand for remanufactured diesel particulate filters (DPFs) for heavy goods vehicles has grown significantly, in line with increasingly stringent EU emissions legislation.
DPF cleaning, remanufacturing and inspection services is a compelling example of the circular economy in action.
First it’s a matter of exchange, where batches of dirty DPFs are collected from customers in the UK and mainland Europe and replaced with ‘truck ready’ remanufactured units on a scheduled basis. This contract-based approach ensures vehicle downtime is minimised and customers achieve value through economies of scale. On arrival at the facility, each DPF is given a unique barcode, enabling it to be tracked throughout the cleaning and inspection processes before it is dispatched in specially designed reusable packaging.
Proprietary cleaning
Cleaning and remanufacturing commences with a goods-in visual inspection to identify any damage to the unit that prevent its further use, followed by a face wash of the DPF to keep particles from contaminating the working environment. The company’s patented proprietary cleaning process, which uses an innovative combination of de-ionised water and compressed air, removes accumulated soot and ash deposits within the DPF. This is a fully-automated process that provides rapid processing and excellent first pass cleaning results. As the deposits are suspended in water during cleaning, there is no risk of particulates entering the atmosphere.
This process removes between 350-450g of soot and ash from each filter, which is up to 30% more effective than other cleaning methods in the market that use compressed air or other water-based methods. The cleaning restores the DPF to at least 95% of its original brand-new functionality, avoiding the need for customers to buy an expensive replacement unit. The soot and ash deposits are collected to form a ‘filter cake’ of particulate matter, amounting to 30 tons per year. This is transported to a waste management partner for further treatment before disposal as non-hazardous waste at a licensed landfill site.
Internal examination
After cleaning, the DPF is machine dried and then quality checked with a patented automated inspection technology. This uses light transmission to verify a DPF’s internal condition. This technology provides an image of the internal structure of the filter, identifying any blockages, exotherm damage and cracks. Identifying this damage ensures the unit is not reinstalled on a vehicle which may result in expensive damage to the exhaust system.
The technology also gives visual confirmation that the filter has been cleaned effectively. The system generates a unique record of the DPF’s condition every time it is cleaned, enabling filters to be monitored throughout their service life.
Further specialised DPF inspection and testing processes are available, if required. These determine catalyst efficiency and for closed-end DPFs use a stream of benign particles to examine the integrity of the ceramic substrate within the DPF.
In addition to cleaning and inspection, any structural repairs to a DPF’s external metal casing can be carried out to ensure units are returned to customers for reinstallation with all components and mounting brackets fully repaired.
DPF cleaning and remanufacturing provides HGV operators with a more sustainable and faster turnaround solution to keeping their vehicles environmentally compliant and operating efficiently.