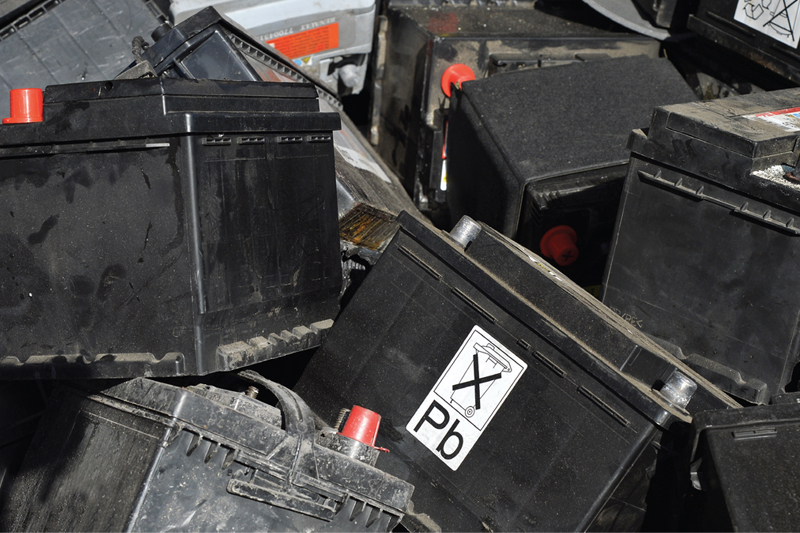
John Bentley, Ecobat’s technical manager, looks at current battery technologies and the recycling challenges posed by them.
Of the many and varied components utilised by vans, trucks and buses on the UK’s roads, the battery is possibly one of the most difficult to evaluate in terms of its quality, as visually, whether premium or substandard, they all look virtually identical. However, with batteries, the phrase ‘you get what you pay for’ is particularly pertinent, because it’s what’s in the case that makes all the difference.
Although absorbed glass mat (AGM) and enhanced flooded battery (EFB) batteries are very much in the spotlight due to increasing electrical demands, the traditional starter, lighting and ignition (SLI) battery is still the most common aftermarket replacement, not just here in the UK, but throughout Europe.
Inside story
From the outset, it is worth clearing up a point of confusion, which is, whether SLI, AGM or EFB, all are lead-acid batteries and the underlying principle to how they operate, remains the same, as within the case are situated six ‘cells’ that each provide 2.2 volts and which, joined in series, provide the 13.2-volts that generally constitute a ‘fully charged’ 12-volt battery.
In a typical SLI battery, lead and sulphuric acid/de-ionised water solution (the electrolyte) make up the primary elements within the case, which must be nonconductive (to electricity) and naturally, acid resistant. Each cell consists of lead and lead oxide electrodes in the form of plates, the number, design and quality of which define the performance of the battery.
The lead provides the negative electrode, the lead oxide the positive, which when submerged into the electrolyte causes a chemical reaction that ultimately produces electrons that provide the battery’s power, directed to the conductive positive and negative terminals.
AGMs on the agenda
The chemical reaction produced within the cells slowly causes the lead and lead oxide to combine with the acid to become lead sulphate, which gradually reduces the electrons that can be produced and therefore, the efficiency of the battery, as it discharges.
However, when the battery is recharged, the lead sulphate is restored back to lead on the negative plates and lead oxide on the positive plates.
When it comes to AGM batteries, the fundamentals remain common to their SLI cousins, apart from the fact that they are termed valve regulated lead-acid (VRLA) batteries because they are sealed and recirculate the hydrogen/oxygen gas produced during recharging within the case, rather than allowing it to escape through a vent and the electrolyte liquid is absorbed into a micro-fibre mat, as opposed to being free to move.
The pure-lead plates within an AGM battery are very thin and, as they are separated by a layer of micro-fibre mat that is also very thin, it is possible to fit several plates into each cell, providing a greater total lead surface area for faster enhanced charge, which reduces internal resistance and boosts the battery’s efficiency.
However good and whatever their construction, over time and use, batteries do eventually need to be replaced, so what can be done with the spent battery?
95% success rate
With environmental concerns quite rightly much more in the public eye, the aftermarket is also far more environmentally aware and committed to play its part. It is therefore crucial for suppliers to offer a reliable waste management policy that ensures that the environmental and legislative responsibilities of those selling batteries to their trade customers are taken seriously and fulfilled completely.
As a member of a wider group, Ecobat Battery, for example, can bring considerable benefits to its customers, not least in being able to state that its ‘closed-loop’ waste management policy ensures that more than 95% of each battery it collects is recycled.
This is only possible because of group companies that specialise in all the processes that are necessary to enable automotive, commercial vehicle and related batteries to be recycled fully and responsibly.
As intimated earlier, lead-acid batteries can be almost completely recycled because when dismantled, the three main elements can be efficiently processed and then resupplied into several industries as important core products. These include the sulphuric acid in the battery’s electrolyte, which is recycled into gypsum for the building industry, the polypropylene battery cases that are recycled into a host of products including food containers, garden equipment and of course, new battery cases, and the lead, which is smelted to be supplied primarily as lead ingots to many of the world’s leading battery manufacturers, and also as lead strip, wire or shot for many other industries.
Bonus for workshops
Turning to alternative technology, clearly electric vehicles (EV) are making the headlines, and many are interested in how the world will handle the end-of-life of EVs most important element – the battery. Although enormous strides have been made to EV battery capability and lifespans, the initial production and final disposal plans have not progressed as quickly.
The lithium battery, which is generally the battery of choice for vehicle manufacturers globally, is an incredibly effective power storage solution. However, it is expensive to produce and, in stark contrast to lead-acid batteries, recycling it is difficult.
Difficult, but not impossible as Ecobat has been diagnosing, disassembling, discharging, re-engineering and recycling lithium batteries for some time and by September 2022, it had processed more than 2,000 batteries, which, bearing in mind that all lithium-ion must be transported under strict dangerous goods regulations, is no small achievement. Furthermore, to ensure it can offer a fully compliant transportation service, it helped to develop a special critical battery transportation box that can be deployed in the event of batteries being damaged or potentially liable to thermal runaway.
Lithium challenge
This work has positive implications for the independent sector because, although its service offering is mainly focused on original equipment manufacturers that have an extended producer responsibility for their batteries from installation in the vehicle to responsible end-of-life recycling, the company is aware that forward thinking independent workshops do not want to be left behind when it comes to the service and repair of EVs.
Through its battery collection and recycling division, the company can safely dispose of any of the batteries the independent sector is likely to come across, including lithium-ion, which is one of the obstacles that has previously held companies back from EV maintenance and repair.