Farécla discusses changes in abrasive technology
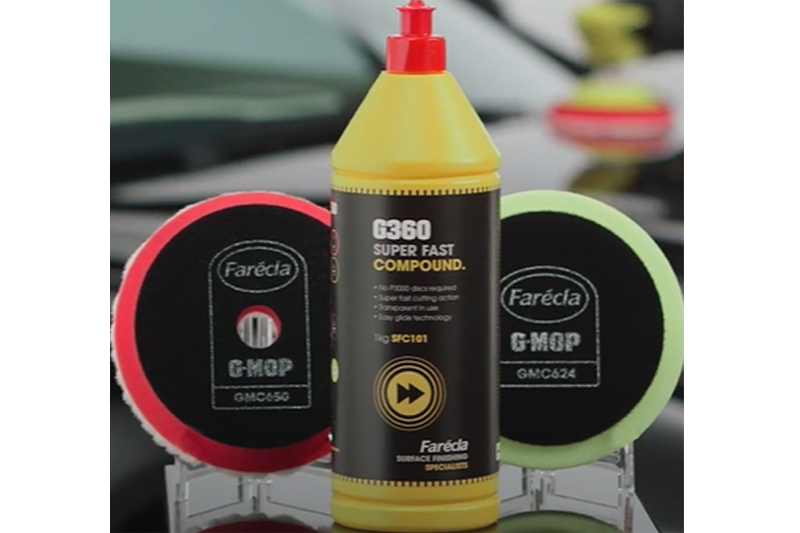
CVW gets an update from polishing and compounds pioneer, Farécla, and discovers how a scientific breakthrough in polishing and a process change have combined to save bodyshops time, energy and product.
With bodyshops under ever more pressure to cut costs, any process improvement that can help the bottom line is of course welcome. But at first glance many, us included, would not think of post-paint defect rectification as an area offering much scope for significant savings, as polishing is a relatively small part of the overall repair cost. Not so, according to Farécla, on account of a scientific breakthrough in abrasive technology that lies at the heart of the company’s flagship polishing system.
Multiple benefits, new technology
According to the company revolutionary tailor-made abrasive particles in its G360 super fast compound (combined with its dedicated super high cut pad) have brought the unique benefit of enabling the system to polish out P1500 scratch marks to a permanent finish faster than competitors can sand to P3000 and then polish. This seemingly impossible feat is a development which is turning the previous tide of sanding to ever finer grades – despite the expense – in order to maintain key to key times in the face of ever harder paint systems coming on to the market.
Thanks to the new technology the system has been tested to be 35-48% faster than its main rival on standard clearcoats, varying with paint surface and operative. So that also means energy savings per job and the opportunity for increased throughput.
Reducing product consumption
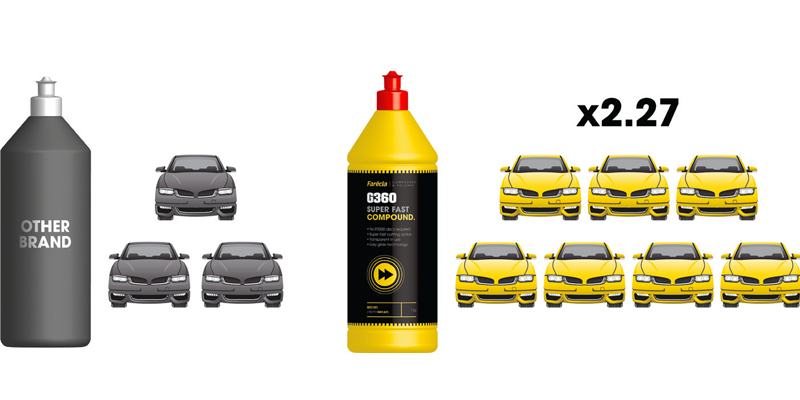
Changing the curve
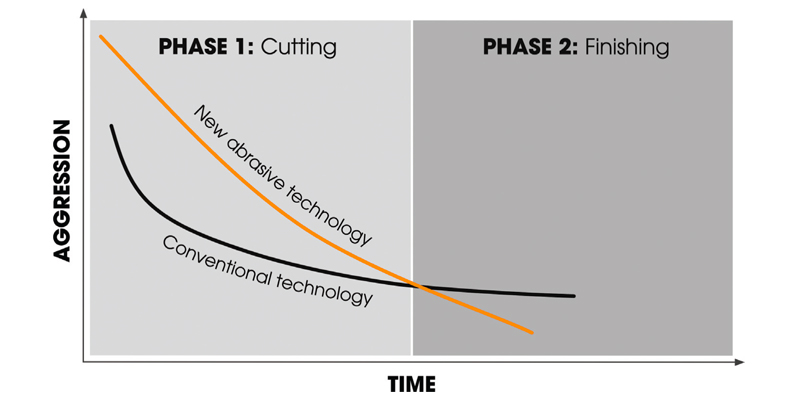
Less product use
The latest trend, driven by the energy cost crisis – towards low energy (air dry) clears has not changed the central precept of the process improvement. Extensive trials and research confirm that DA sanding with P3000 or finer grade discs is not necessary, as it can be replaced with a rotary polishing step using G360 on its super high cut pad albeit the recommendation for cured low energy clears is sanding to P2000 rather than P1500.
Still more cost savings come, says Farécla, from reduced product expenditure. Live data from a six-month bodyshop trial found that the new system required 56% less product per job compared to its main rival, and that’s before considering the cost savings from eliminating or severely reducing the use of expensive P3000 discs.
A ton of savings
Marketing manager, David Stokes explains: “Data from the extended trial conducted at an A-grade bodyshop group concluded that the number of jobs done by a bottle of G360 would previously have required 1-1½ boxes of P3000 discs. That’s a huge saving. At today’s prices for a shop that changes process and switches away from P3000 that’s equivalent to each bottle having around £100 in cash for your bottom line strapped to the bottle, just for the savings on P3000. Then add to that the energy savings from getting each job done so much faster and the attendant opportunity for more throughput, plus the fact that you could now be using less than half as much polish per job, and the financial advantages start to look irresistible.”
Perhaps, a less easily measurable financial benefit of the system is the reduction in reworks reported by very many of the users who make the process switch. One concrete example, however, is a high-volume de-fleet centre for which the number of reworks was a major headache. Plagued by scratch marks reappearing, the site bodyshop manager really appreciated the absence of fillers in G360 which enabled “right first time” permanent finishes. Comparative data shared from pre- and post-switch financial periods showed a reduction in post-paint sanding and polishing materials expenditure of 64%, and even better, an increase in throughput of 30%.
Diminishing abrasive theories
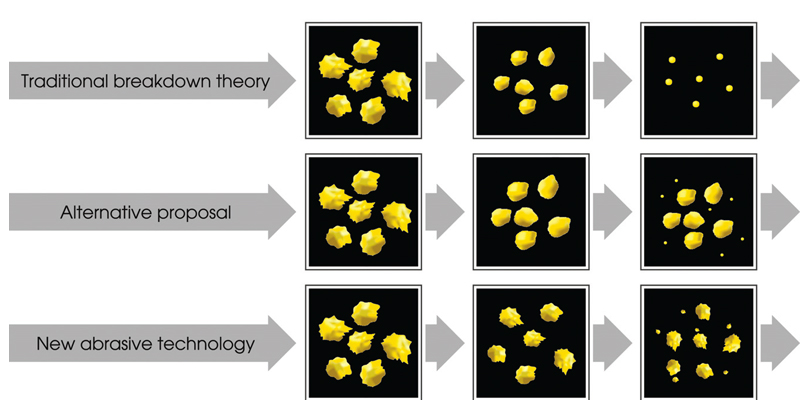
Sanding and polishing energy usage post-p1500 sanding
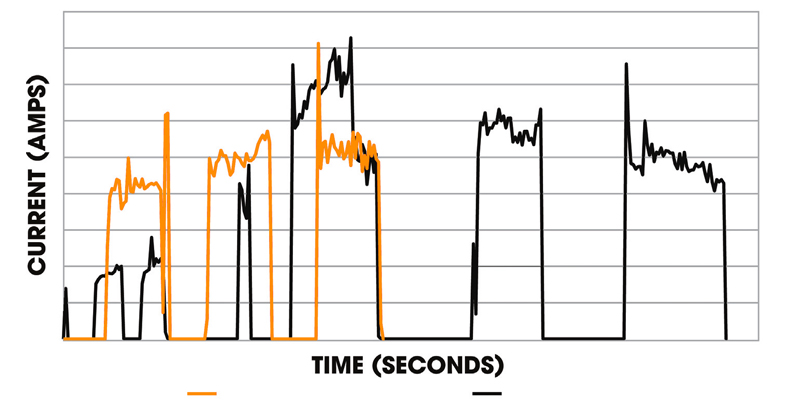
Calculate the odds
To help bodyshops, Farécla has created a savings calculator. This allows the bodyshop to input its own specific circumstances and see the potential savings that the process change could add to their bottom line, often a five-figure sum for a shop that is moving away from P3000.
Practical benefits
When asked about the practicalities of the system we learned from applications and training manager, Mark Taylor that the bodyshop owner and manager are not the only ones to benefit from the new technology. “When you sand with P3000 you make the area to polish four, even five times greater than the actual denibs, whereas with G360 you are laser focused on those small P1500 denib scratch marks. It’s like keyhole surgery versus open heart. And not only that, the new system gives the operative a whole lot more control as well. When you flat an area with P3000 the P1500 scratches are obscured beneath the matted area so you can’t be certain whether you have sanded for long enough to remove them all, and if there are P1500 scratches remaining you will spend a lot longer polishing. By contrast the G360 system develops a transparent film in use that lets you see the scratch marks disappearing, so you always know where you are in the process.”