How are oils and lubricants made?
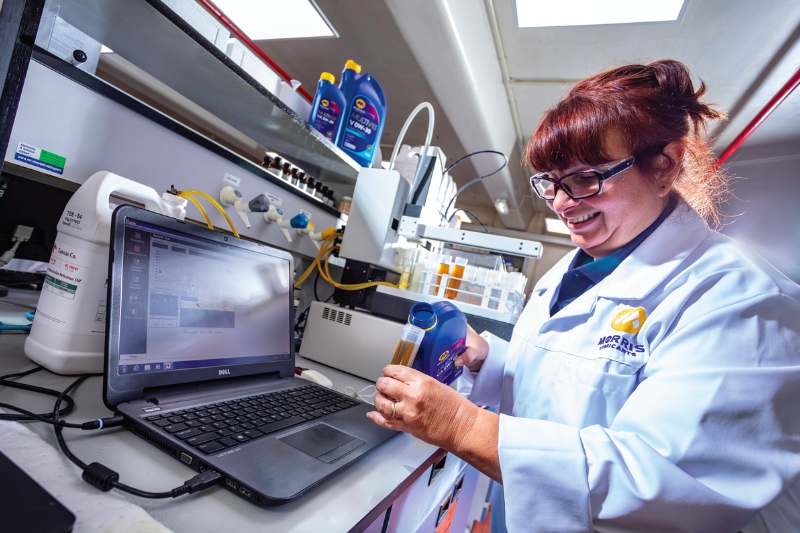
Ever wondered how oils and lubricants are made? Adrian Hill, technology manager at Morris Lubricants, offers a behind the scenes look at how today’s products are the result of painstaking development and testing.
To fully protect commercial vehicles, it is essential to use oils and lubricants that comply with the manufacturer’s specifications. Having oils and lubricants available to carry out a multitude of tasks under a myriad of different workloads is the accumulation of years and years behind the scenes development. A well balanced and validated oil and lubricant formulation doesn’t just happen, there is a process and a very precise one.
What’s at stake?
New oils and lubricants are developed and formulated when a demand arises, usually from the requirements of the OEM. This may be driven by a new engine or transmission design for example, or if a different workload is being introduced, maybe even a different type of fuel. The OEMs work with the leading technology providers in the lubricants industry, who develop or even create innovative chemistry.
These technology providers in turn work with approved base oil manufacturers. Base oils can be derived from mineral sources (crude oil), synthetic sources (chemical synthesis), or renewable sources (biodegradable oils). Each type of base oil has its own set of properties that affect the performance of the lubricant. The choice of base oil depends on the specific requirements of the application. The technology providers and the approved base oil manufacturers deliver a powerful combination of expertise to develop the precise formulation.
The base oil provides a protective film across a wide temperature range, ensures proper heat control, contributes to fuel efficiency and more importantly carries the additive chemistry to all the system components. These chemical compounds are added to the base oil to enhance and refine its performance. Common additives include anti-wear agents, friction modifiers, antioxidants, corrosion inhibitors, detergents and dispersants. Each additive serves a specific purpose, such as reducing wear, preventing oxidation, or keeping the engine clean – it’s a long list. Fine tuning the combination of approved base oils and additive chemistry is a lengthy and costly process. The different formulations must also carefully balance the approved base oil and the specific additive chemistry to ensure they work synergistically without causing adverse effects.
Testing and optimisation
This combination of approved base oils and additive chemistry is a dynamic process working with the OEM. Feedback is provided to the OEM, who in turn make critical judgements on the formulations being made. A testing regime is initiated that consists of laboratory bench tests, static rig tests and field trials. The laboratory bench tests measure properties such as viscosity, volatility, cold flow, pour point, flash point, and thermal stability. The results help identify any weaknesses in the oil and lubricant formulations and make necessary adjustments.
During the static rig tests the oil and lubricant formulations are subject to a series of severe workloads. In essence the engineering department are trying to break the engine or transmission and the chemists are devising oil and lubricant formulation strategies to stop this from happening. In the case of engine oil testing, the engine is coupled to a computerised system which can add varying loads, adjust speeds, sometimes at reduced oil levels, to simulate worst case operating scenarios. Once an oil formulation measures up to these tasks, real world testing is the next step via field trials.
The field trials phase involves using the oils and lubricants in actual commercial vehicles to assess performance under typical operating conditions. Field testing provides valuable data on the oil’s and lubricant’s durability, efficiency, and overall effectiveness. Any issues identified during this phase are addressed through further formulation adjustments and testing. OEMs have their own approaches, but in the case of engine oils, this may include vehicle fleets employed in various duty cycles, long haul, stop-start etc. This can be a lengthy process that may take up to three years, as a certain number of road miles or operating hours must be achieved. At the end of this period the engines are stripped and inspected and scrutinised. If the findings comply with the OEM’s parameters, then formulation is approved to work.
Compliance and sustainability
After all the tests have been passed and having a formulation that works in its intended application is still only part of the development process. Before the formulation is released to the aftermarket, where it can be manufactured in commercial volumes for the end user, its environmental credentials also have to be assessed. Can the components be manufactured in a sustainable way that minimises any environmental impact? Do the oils and lubricants, once blended, have any hazards that may affect how it is handled by the end user? Is any specific labelling required or handling instructions that need to be communicated? Once all these boxes are ticked, the end user can begin to enjoy this new technology.
To sum up, the development of oils and lubricants is a precise and multi-faceted process that requires a deep understanding of chemistry, engineering, industry and environmental requirements. From initial formulation to final production, each step is crucial in creating oils and lubricants that deliver optimal performance and reliability. As technology advances and new challenges arise, the development of oils and lubricants continue to evolve, driving innovation and efficiency. Only by using approved base oils, quality additive chemistry and following the correct validated formulations agreed by the OEMS can you be confident that the final oils and lubricants produced are going to perform as they should.