How can tool manufacturing be more sustainable?
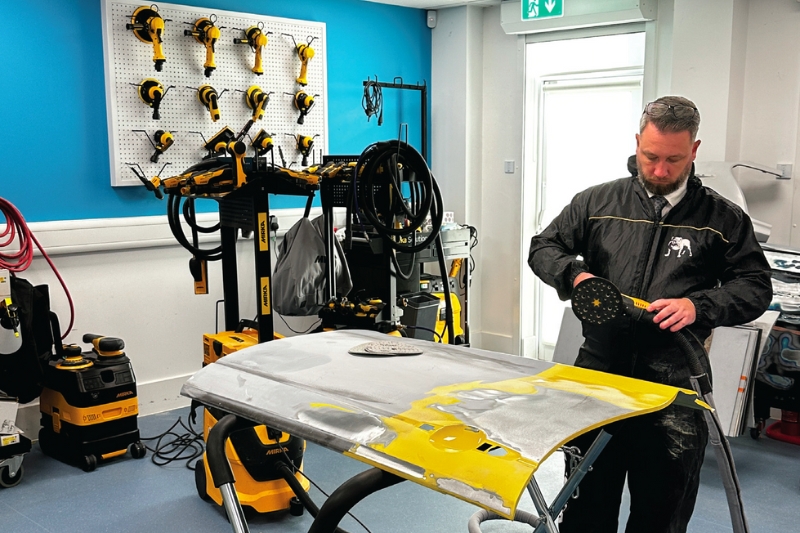
CVW popped along to Mirka’s recent press event to find out what is happening on the tools, abrasives, and polishing front and talked to Steve Smith, national sales manager Collision Repair. He shared some insights about the company’s growing product portfolio and its steadfast commitment to sustainability.
‘‘When it comes to sustainability, Mirka’s philosophy is anchored to three key pillars, which are societal impact, environmental cleanliness and resource efficiency. These are significant focus areas, so let me break them down for you,” began Steve.
“For environmental cleanliness, we are aiming for a 55% reduction in greenhouse gas emissions by 2035 and we are also aiming to achieve net-zero emissions by 2050. We believe we are on the way to meeting these targets and we are always looking into options to help us get there. With resource efficiency, we are talking about the lifecycle of the product and what happens to it when it is ‘finished’. As a business, we want to ensure we get the most out of our products and this is highlighted by the fact that we are looking to have 70% of Mirka’s products recyclable by 2035. This aim is supported by a €25m circular grain manufacturing plant in Finland, which is scheduled to be operational by December 2025. The site has been designed to sort, clean and prepare incoming recycled materials as well as screen and classify grains for reuse. This will aid in maximising the lifecycle of products and reducing waste both internally and from external sources.”
For societal impact, the company is aiming for zero workplace accidents and the provision of dust-free work environments because, as is common knowledge, the dust produced can affect the health of employees and be detrimental to jobs being performed in the workshop. Steve goes on: ”As a business Mirka maintains a constant dialogue with customers through our team of experienced technical experts and information gleaned from the conversations is circulated to the R&D team based in Jeppo, Finland to help it design innovative and versatile tools tailored to industry needs. In 2024, several groundbreaking products were launched, offering substantial benefits to commercial vehicle workshops.”
The first was the DEROS RS 600 rotary sander. This tool has a user centric design that combines power and precision to make easy work of multiple applications including paint removal from metal panels and coarse grinding sanding. In addition, its lightweight, compact design provides a smooth operation and enhances user comfort and productivity, despite it being a powerful heavy-duty sander. In addition, it has Bluetooth connectivity, so when it connects to the myMirka app users have access to real-time data about the tool and how it is being used.
Cordless convenience
The second tool was made up of two tools from the same product range. The Mirka FBS-B 13 and FBS-B 10 have been designed to make cleaning up welding seams and spot welds easier and more efficient. The Mirka FBS-B 13, designed for wider belts, and the Mirka FBS-B 10, designed for narrower belts, both provide the user with rapid and efficient material removal and can handle multiple demanding applications with ease. Because the sanders are both cordless, accessing difficult spots to work in is easy as there are no cables or hoses hampering their access, so jobs are completed quickly.
“Alongside the evolution of tools, we are seeing certain trends come to the fore and one of them is running costs. As a manufacturer, we are aware that this trend is at the forefront for businesses and we have identified savings that can be achieved by considering the use of a mobile extractor versus an integrated unit,” continues Steve.
“Mobile dust extraction systems are now a cost-effective option and do a good job in reducing dust in the workshop. They also reduce energy usage because they only draw electricity when they are in use, which can lead to significant savings when compared with the cost of running a central vacuum system. Additionally, Mirka’s dustfree sanding solutions significantly reduce dust production by over 90%, minimising contamination risks and lowering valeting costs. In addition, when the Mirka Abranet range of abrasives is paired with Mirka sanding tools and extraction units, they enhance workplace safety, boost productivity, and improve profitability.”
Responsible actions Mirka says its dedication to innovation and sustainability ensures it remains a trusted partner in the collision repair industry. In addition, through the delivery of the next generation of tools and embracing environmental stewardship, it claims it is not only enhancing customer value but also building a more resilient and responsible future for the industry.