Identifying and avoiding adjustment issues
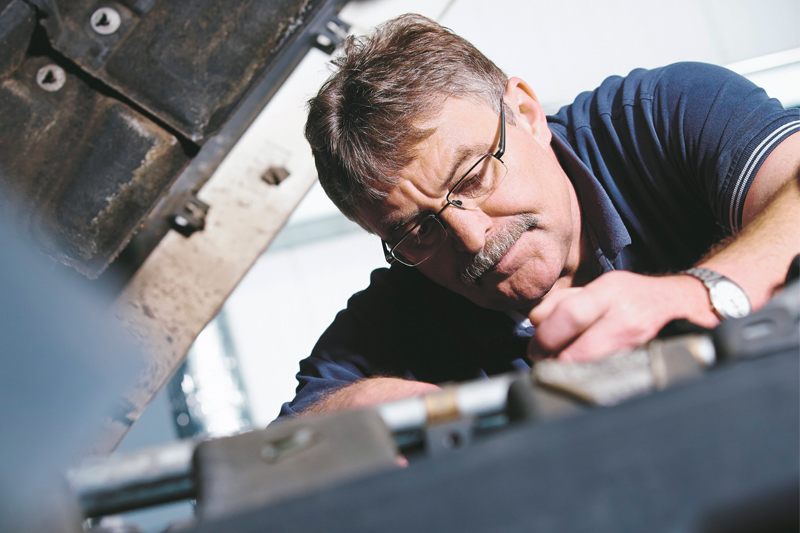
It’s been said that you can spot adjustment issues if you notice slack adjusters that are extended at different angles on the same axle. Avoiding those problems starts with the right maintenance. Here BPW offers some guidance on its ASAs.
The BPW drum brake is a simplex (single camshaft) ‘S’ cam operated unit that comes in three sizes – 420mm, 360mm and 300mm. The camshaft is supported by two bearings.
The outer bearing (bush) is of rolled non-ferrous construction and has grease ways rolled into it. The grease is contained in reservoir holes punched through the bush. The grease is applied through a grease nipple positioned just behind the brake back plate. (Fig. 1)
Grease is the word
BPW ECO Li Plus grease should be applied until fresh grease emits through the dust cover, with the period of greasing being a maximum of 12 weeks. There is an ‘O’ ring positioned near to the outer edge of the bush to prevent grease from escaping into the drum and contaminating the friction surfaces.
The inner bearing is made of sintered steel and is a self-aligning spherical design. The bush has grease ways and reservoirs formed into it during the sintering process. The bearing is held in place by half shells bolted to the inner camshaft bearing bracket. A grease nipple is provided, and the level and period of lubrication is the same as for the outer bush. (Fig. 2)
The camshaft is connected to the air chamber by an automatically adjusting slack adjuster. The slack adjuster is located on the splined end of the camshaft and is secured by a nut. Again, a grease nipple is provided for lubrication, and this follows the pattern previously mentioned. (Fig. 2)
The key to long life and efficient operation of this system is correct lubrication and adjustment. Correct inservice adjustment of the brake should be checked periodically: with the brake released, the pin and pointer on the side of the slack adjuster should be exactly in alignment. (Fig. 2a)
Note: If this is not the case, then it will not be possible for the slack adjuster to auto-adjust properly and BPW should be contacted for advice before proceeding further.
Free play
Assuming that the pin and pointer are correctly set, then the most convenient way to adjust the free play is to use a good quality 19mm socket to wind on the brake clockwise until it just binds and then release the brake by turning a minimum half turn (180°) anti-clockwise (Fig. 3). The adjusting bolt is located under the plastic dust cap on the outer face of the slack adjuster body.
Note: To back off the brake, the adjusting bolt has to be rotated anticlockwise, and to do this the socket has to be pressed into the slack adjuster quite hard against a spring to release the clutch. If you try to force anti-clockwise rotation without depressing the internal clutch, then the mechanism will be damaged.
The slack adjuster should be checked every six months to ensure that the automatic adjustment is working correctly. To do this, remove the plastic dust cap and wind off the brake by turning the adjusting bolt approximately one and a half turns anticlockwise. Then, either by hand or by having an assistant operate the foot brake, apply and release the brake half a dozen times.
You should be able to hear a definite click as the slack adjuster over-strokes, and when the slack adjuster is on the return stroke, you should see the adjusting bolt wind on clockwise. It is a good idea to purge fresh ECO Li Plus grease through the slack adjuster whilst carrying out this procedure as this ensures that the grease finds its way around the internal clutch mechanism.
Always remember to replace the dust cap after any adjustment, and if the cap is damaged, new ones can be obtained. If dust and dirt are allowed to get into the adjuster port this will lead to premature failure of the unit. Remember to adjust the brake before the vehicle goes back into service.
Lubrication point
An often-neglected lubrication point is the clevis pin which connects the slack adjuster to the brake cylinder pushrod. This should be kept greased to prevent seizure which will degrade brake performance.
After a number of years, wear will take place predominantly in the outer camshaft bush and on the camshaft. This wear can be tested by placing a pinch bar under the camshaft behind the brake backplate and on the top of the suspension clamping plate. If excessive lift is shown, then the camshaft and bushes must be replaced.
Camshaft bushes are available as a BPW kit that contains enough parts to refurbish the complete axle. Camshafts are obtainable singly and are handed. It is advisable to replace both camshafts across an axle and bushes at the same time.
When carrying out a brake re-line, make sure to remove the brake rollers and lubricate the brake roller bushes with BPW’s ECO Li Plus grease.
Do not put any grease on the head of the camshaft. When re-lining brakes, always fit a new brake shoe pull-off spring. Finally, in the UK we fit a pull-off spring between the slack adjuster and the air chamber bracket (Fig. 4).
These springs should be renewed at every brake reline, and always use the special hole provided in both the slack adjuster arm and in the brake chamber bracket.
The BPW automatic slack adjuster requires some knowledge and understanding when replaced. In-service testing and functionality checks are mandatory to ensure compliance and correct operation.
- Brake chamber push-rod length movement when the brake is applied from static should be checked dimensionally against the brake calculation lever length – typically 15- 22mm movement, 10-15% of the effective lever length.
- Manual intervention should not be required if the adjuster is functioning correctly. The free play should conform to the above dimensional requirements.
- If it doesn’t, a functionality check should be carried:
- Having fully depressed the adjuster collar using a good quality 19mm socket, de-adjust the brake with the hub spinning free approximately three quarter of a turn, or at least 50mm of free play.
- Operate by hand several times and on return, adjustment should take place, the adjuster bolt turning in a clockwise direction and the adjuster collar ratchet should be audible.
- If the free play is not taken up and combined with no audible adjustment, replace the BPW slack adjuster with BPW OE product.
- The adjuster must be replaced in accordance with the BPW maintenance instructions.
- The set-up procedure must be followed, paying particular attention to:
- The adjuster pin and pointer.
- Wear indicator positioning.
- Final tightening sequence of the securing nut and spherical bearing.
- Lubrication using BPW ECO Li Plus grease.
- Re-attaching the sealing rubber cover.
- Final brake adjustment to a minimum half turn (180°) anticlockwise from a binding brake.
- Good practice would be to undertake a laden dynamic brake roller test to confirm compliance with the required minimum brake forces and imbalance allowances across all axles of the trailer.
Brake adjustment
Set the free play by disengaging the clutch on the slack adjuster and turning clockwise using a good quality 19mm socket until brake bind is achieved, proceed to turn 180° anticlockwise to achieve between 0.7- 1mm lining to drum clearance. Position the brake lining indicator in the vertical position and tighten the camshaft nut to its required torque.