How to comply with the ‘meaningful brake test’
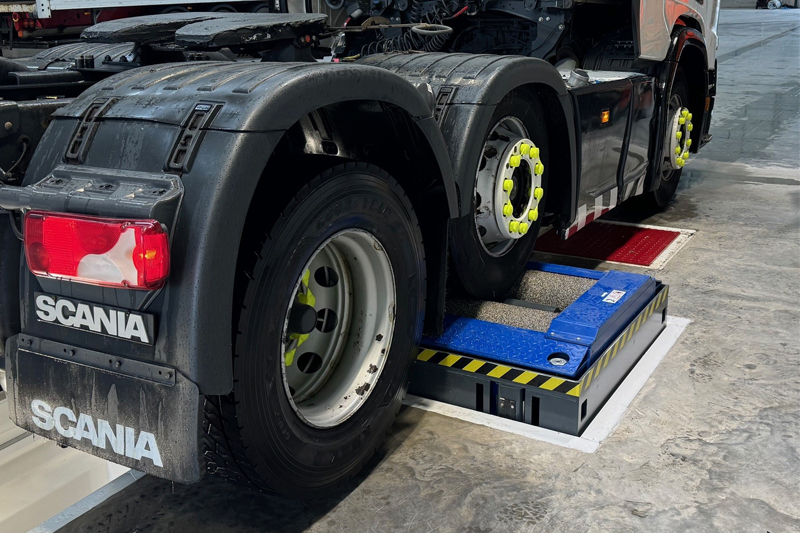
This year sees the introduction of the ‘meaningful brake test’. MAHA UK managing director, Neil Ebbs, offers some guidance in complying with the new guidelines.
With the impending introduction of the ‘meaningful brake test’, set to take effect in April 2025, brake testing procedures will see significant changes: laden roller brake tests will, with some exceptions, be the only accepted methods for brake testing.
To prepare for this change, it is strongly advised that workshops conduct laden roller brake tests at every safety inspection.
Achieving accurate and reliable brake tests is essential for road safety. Every workshop faces unique challenges, and a one-size-fits-all approach is insufficient. Recognising this, MAHA UK offers tailored brake testing solutions that ensure compliance and address a range of needs – vital with the ‘meaningful brake test’ being enforced in April 2025.
Base station
One solution is the MBT 7250 commercial brake tester. This model is widely used in Driver and Vehicle Standards Agency (DVSA) and authorised testing facility (ATF) stations. It is recognised for its precision in measuring brake system performance.
Featuring a large roller sensor with a 100mm diameter and an axle load capacity of 20 tonnes, the MBT 7250 offers comprehensive coverage across each tyre’s dimensions. Beyond its core features, the MBT 7250 is designed for versatility; it can be equipped with additional floor units, allowing it to function as a base module for custom test lanes. The electronic, temperature-compensated strain gauge system ensures accurate measurements regardless of external conditions, thanks to its robust design.
To tackle the variety of challenges faced by different workshops, MAHA UK also offers a MBT 7250 rising roller bed option. Complete with integrated hydraulic rams, these beds can lift the rollers by 250mm with a pull-down force of 10 tonnes.
An optional system, compatible with existing MAHA IW7 frames, will raise rollers by 180mm but with a pull-down force of five tonnes. This provides flexibility to meet diverse workshop requirements.
In scenarios where simply elevating the roller bed and brake tester is insufficient, MAHA UK offers several options: fixed points can be installed in the inspection pit, or hydraulic rams – either fixed or movable – can be employed when split bed across a pit. For additional flexibility, a rail system with a movable dolly may be utilised, especially when no pit is present.
While no single system is universally applicable, many tried-and-tested options are available. If a high percentage of vehicles can be successfully tested, then our solution is a good choice.