A guide to helping your workshop go green
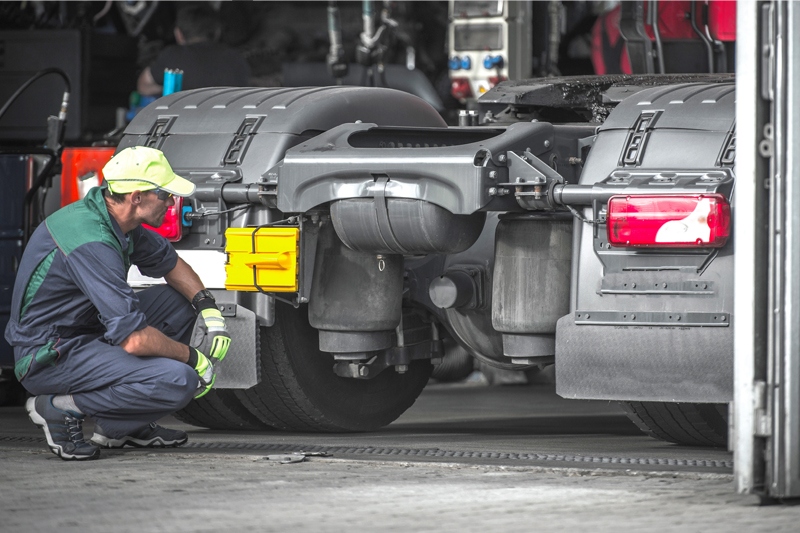
Want to make your workshop more environmentally friendly, produce less waste and be cheaper to run? Witham Group’s MD Nigel Bottom offers some green tips.
Going green in a workshop is always a team effort but transitioning from conventional raw materials to non-toxic materials is one of the hardest areas a garage must consider.
Workshops and garages traditionally use chemicals and fossil-based products like engine oil which are essential to their business and for the vehicle or machine to run properly. Unfortunately, these are not usually environmentally friendly products but there are ways you can identify and promote a greener culture in a workshop by working a little smarter.
When looking at green credentials, you have to look at the full package. Not only the more common elements of sustainability but also right back to your supply chain and the products and services you operate within.
Energy
Review the efficiencies of lighting, heating, ventilation, cooling systems, insulation opportunities, water use, and pollution control. Ideas you might want to consider include:
- Installing solar panels on workshop roofs and depots – they often cover a wide surface area and can help generate new power to heat and light buildings and machinery and equipment.
- Harvest rainwater from the roofs and collect in IBC containers. Use the water to wash and clean vehicles and other equipment throughout the year. Thousands of litres of water can be saved each year.
- Install PIR lighting so no lights are on unless they need to be.
Products
The choice of lubricants that a workshop uses are wide and varied but can you ensure that suppliers offer the following to help you achieve your own green goals:
- Biodegradable alternatives. For example, Witham’s range of multi-purpose lubricants which uses sheep’s lanolin as the strongest, natural lubricant nature can supply. This has been captured and blended to produce a range of five viscosity oils, from light work like chain and maintenance oils to restoration rust preventers and anti-seize greases, which are not only biodegradable but extremely long lasting, non-toxic and food and water safe.
- Other greener alternatives such as biodegradable chain oils and hydraulic and tipping oils are extremely popular and give comparable performance to more traditional mineral counterparts. In addition, there are now alternative fast-acting, biodegradable liquid floor degreaser detergents, offering ultra-powerful, deep cleaning of workshop floors. They are specifically designed to remove general dirt, tyre scuff marks, silicone film and are an effective degreaser for fats, mineral and synthetic oils, and greases.
- Engine oil viscosities. Lowering CO2 emissions and improving fuel economy is high on the agenda of LCV/HGV owners. Swapping lubricants to a fuel-efficient approved alternative can deliver more than 1.5-2.5% fuel saving if carried out correctly. Lower viscosity lubricant sales are on the rise and choosing the right engine oil can make a real difference to emissions and carbon impact and also for the business owner.
Packaging
Purchase not only fully recyclable packaging, but container plastic packaging from some suppliers that are now made from at least 30% recycled materials.
- Choose a lubricant supplier that offers recyclable or recycled packaging.
- Recycling schemes are also available for bulk 200 litre barrels.
- Partner with local recycling and waste suppliers – many schemes are available nationwide.
Bulk storage tanks
Workshops and garages tend to use a lot of the same lubricant products and can have piles of used plastic containers lying around the place, so consider installing bulk storage tanks. Your lubricant supplier can advise on the best way to install the tanks. Lubricants are filled up in the colour coded tanks as required, and the tanks have sight gauges, taps, or pumps and come labelled with the different product names and their application.
Simple, clean and easy to use, these tanks help keep your working space shipshape and avoid spills from containers. They also help avoid important oil contamination and help the environment by using less packaging. They also provide important health and safety requirements for lubricant storage. Using bulk storage tanks across all the workshops and garages in the UK would save thousands and thousands of plastic and metal containers being sent to landfill and would save on waste collection costs and administration.
New technology
You can also make a difference by choosing a supplier where greener technologies and processes are to the fore. After all, how lubricants are manufactured is changing – this alone can be one of the most beneficial of savings to a workshop environment due to the reduction of carbon footprint levels. The necessity to improve both the time, cost, and environmental impact of the lubricant manufacturing industry, has driven manufacturers like us to develop and employ innovative new processes.
Ours is called Blendtek and it removes the need for base oils and product formulae to be heated up for long periods of time using traditional gas energy. Instead, thousands of tonnes of high-quality workshop oils using no heat and no agitation can be made using solar panels and a simple 25A plug, saving time, energy and drastically reducing the carbon footprint. To evaluate the savings to the environment, Witham has now saved over 33k tonnes of carbon emissions since using the process and heated the equivalent of over 182 homes in the UK for a year. Our overall gas consumption has been reduced by just over 83% and the technology, the energy saving statistics and the principles of the new ultrasound way of blending is now being shared with the lubricant industry.
This exciting breakthrough is all about changing the environmental impact of lubricant manufacturing in the first place. So many other environmental schemes and businesses look to offset their impact by using carbon dumps or sinks and investing in other environmental and climate protection projects. We have instead, come up with a way that prevents the creation of high energy use in the first place and are proud to lead the lubricant industry with this manufacturing innovation. We believe we are the first company in the world to truly blend in a carbon neutral process. We are determined to help other blenders improve their own sustainability profiles and improve the oil industry’s reputation with substantial impact.
Green credentials
Witham is now the first lubricant blending company in the UK to manufacture its lubricants in a 100% carbon neutral way. The basic principle of ultrasound is to use a high-speed, micro-cinematographic sequence of laser-induced cavitations near to a solid surface. In short – and quantify it – using a traditional blending process (similar to our old plant) using heat to blend and mix generated from gas burners and/or steam from a boiler and standard agitation (paddles) created a carbon footprint of 1962kW per 10,000 litres produced.
Using the Blendtek system, Witham manufactures 10,000 litres of high-quality workshop lubricating oil using no heat and no agitation, and, more importantly, the company only generates a carbon footprint of 6kW per blend.
Ultimately, if everyone looked at their business to see how environmental improvements can be easily made within their business, from what they buy and from whom, workshops and garages could collectively make a huge success of going green. It’s all about small steps that over time can make a big difference.
Put another way, to ask everyone to build a huge brick wall would be daunting to some and impossible for others. However, ask everyone to simply place one brick, one at a time themselves, and encourage their friends to do the same, the wall would build itself. In other words, set an example by going green early!