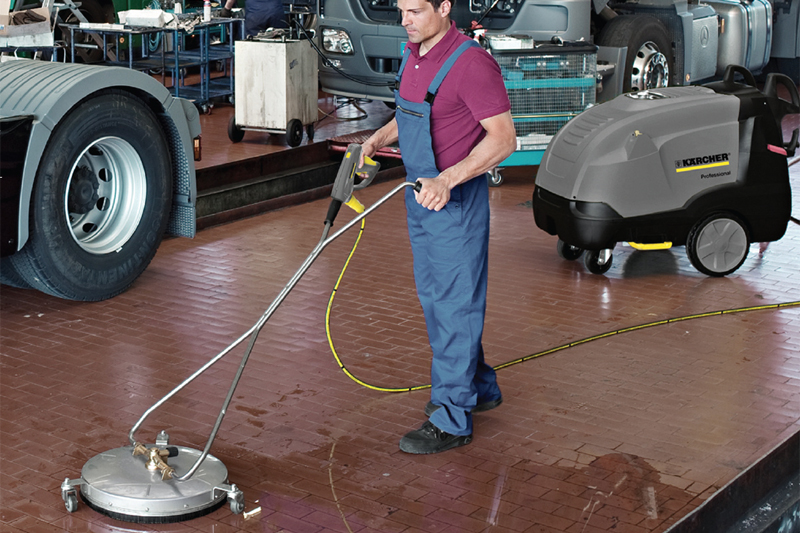
Daniel Took, Head of Professional Product Marketing at Kärcher UK, explores the process for keeping workshops clean and in good working order to prevent undesired health and safety risks.
A messy workshop can quickly lead to an undesired health and safety risk with the potential for trips, slips, and ultimately injuries. To protect yourself and your colleagues, ensuring that the workshop is kept clean is imperative, especially when it comes to floors. To meet standards, weekly routines are ideal, although sometimes a daily or immediate clean can be required.
The amount and type of dirt on the workshop floors will determine the level of cleaning that is necessary. For example, Kärcher’s push sweepers are perfect for picking up loose dirt and debris scattered on the workshop floor on a daily basis; however, for a deeper clean and to target stubborn dirt, scrubber dryers are a particularly efficient and cost-effective solution. The machines can be operated either ride-on or walk behind and are great for surfaces from as small as 200mÇ in size.
The tools for the job
Scrubber dryers use a series of brushes that scrub the floor as the machine passes over the surface, which loosens dirt that has worked its way into the floor. At the back of the machine, the squeegees collect the loosened dirt where it is then deposited in the dirty water tank to avoid contamination with the fresh-water tank. This process has the added benefit of leaving the floor dry after it has been cleaned, allowing you to quickly get back to the job at hand.
Heavily soiled flooring will require deep cleaning which can be achieved using an easy two-step method, which ensures that even the dirtiest workshop floors are returned to their former state. The first step involves the application of a high concentration (5-20%) detergent to the floor to break up the tough dirt particles, such as Kärcher’s FloorPro Intensive Deep Cleaner RM 752, which can be used in any of the scrubber dryers.
The machine can then go over the surface with the scrubber whilst the solution reacts with the dirt. In the second step, the machine collects the dirt and grease loosened by the brushes and solution, where it is collected by the machine’s squeegee and stored in the dirty tank.
For smaller spills, a general maintenance clean is an effective solution. This involves a one-step process using a cleaning solution of 0.5-3% prior to scrubbing the surface and collecting the loosened dirt.
Adjustable attachments can be added to scrubber dryers to improve the end result and to account for the different flooring types typically found in workshops. There are two main attachments to look out for: disc or roller scrubbing heads.
For smooth floors, such as laminated flooring, disc systems are effective. However, most workshops contain structured floors for which roller systems are most effective. The roller systems contain fine bristles that can penetrate the surface of the floor whilst applying greater pressure and higher rotational speed to lift dirt from the surface. Additionally, the high rotational speed (up to seven times greater than on disc systems) allows the brushes to clean themselves by propelling dirt away.
Stoneware tiles
When cleaning stoneware tile flooring it is important to make use of a powerful mechanism and microfibre technology. This is because the micro-pore structure of the tiles attracts dirt resulting in them becoming grey and discoloured. With lots of fine pores to contend with, thicker bristles are unable to penetrate effectively.
The addition of a microfibre roller pad is ideal for stoneware tile cleaning as the strong contact pressure and high rotational speed of the microfibre rollers removes the dirt and immediately expels it from the microfibre material. This means the roller maintains the same efficiency throughout, restoring the tile to its original appearance.
Ceramic tiles
Other popular tiles found in workshops are “orange peel” ceramic tiles (typically reddish-brown in appearance) and these are best cleaned using roller brushes with polypropylene bristles. The bristles work to lift dirt off the surface,which,when combined with a powerful alkali-based gravel, are highly efficient in dislodging grease, oil and brake dust, and mineral soiling.
Cement screed
Cement screed flooring can often be found in workshops and is usually exposed to the elements, coloured with an epoxy resin coating or is treated with a slip-resistant material. To clean these surfaces, a roller scrubber head is essential for getting into the gaps within the concrete where it has dried.
In the current climate, having a clean working area is not just a ‘nice-to-have’. A hygienic workshop not only protects the health and safety of those working within it, it also prolongs the life of the workspace and goes a long way to bolster a positive business reputation.