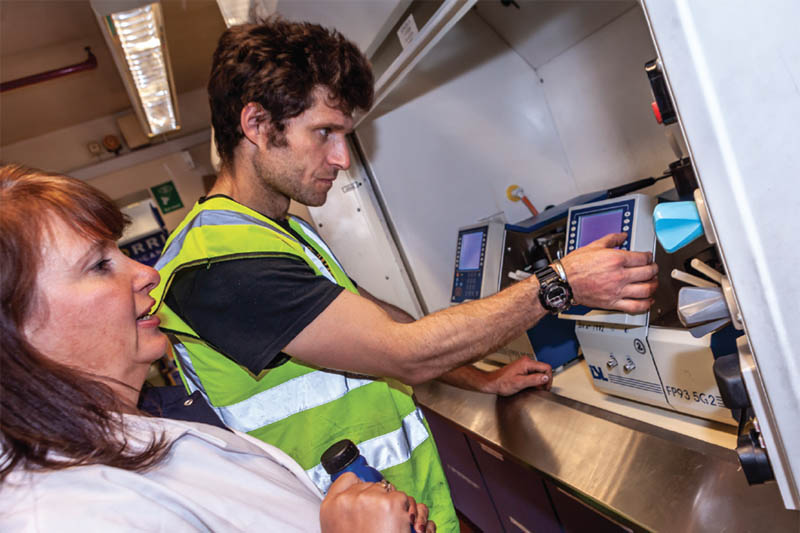
We take a look inside the lab at Morris Lubricants to see the processes that go into producing a quality oil.
At 7am, Laboratory Supervisor Darrell Bates is the first to arrive at the Morris Lubricants laboratory. The room is cool and will stay that way to protect the integrity of samples – over 5,000 are tested and processed here every month. The ambient air-conditioned environment is also a critical safeguard against overheating which could impact the performance of equipment and computer systems.
Employing the use of specialist fluids and internal oil samples, it’s his responsibility to make sure everything in the lab is fully functional and ready for the day ahead. After that, a digital Laboratory Information Management System (LIMS) will take over to track, log, and analyse data, flagging any inconsistencies or anomalies that might be indicative of an issue.
Darrell – who heads a team of four and has been with Morris Lubricants for a total of 32 years – says, despite significant advancements in technology during this time, it’s the staff, including Lab Chemist Thomas Roycroft, that are “the most impressive kit in the laboratory”. Their wellbeing, he says, comes above all else.
Darrell comments: “Within a family-owned company, you are a person, not a number. We have numerous solvents, acids and alkalis, naked flames, and other reagents that have to be used correctly, and with the appropriate personal protective equipment. We also have to social distance and mask up when necessary, with plenty of hand washing and sanitising.”
Dedicated to three key areas – Product Quality Control, Equipment Condition Monitoring, and Product Investigation – and with approximately 650 active formulations in the company’s catalogue, the department’s capacity and capability for testing and product development is considerable. Committed investment in the latest, most-advanced equipment and technologies is a key factor.
“As lubricant specifications move on and become more complex, they often dictate new test methods which require new equipment,” explains Andy Litchfield, who, in his role as Technical Director, oversees the Laboratory and Technical teams, who work together on research, new formulations, and day-to-day testing.
“The Morris family have always purchased what is required because product quality is key to the success of the company, and without the correct test equipment you cannot guarantee the highest quality. Their support allows us to keep up to date and compliant with new and evolving demands.”
With a combined cost of approximately £75,000, recent upgrades include a new Fourier Transform Infrared Spectrometer (FTIR) which is used to identify organic materials and an X-Ray Fluorescence (XRF) machine which measures elemental content so helps the team ensure they are adding the correct amount of performance additive which often contain elements such as calcium or zinc.
The Morris routine
Operating a staggered shift pattern, the Laboratory team processes incoming and outgoing materials throughout the working day. Samples arrive from on-site locations such as blending tanks and filling lines, as well as from customers out in the field. Darrell adds: “We test empty tankers as well as deliveries for moisture and cleanliness. Our products are tested all the way through the process of production, guaranteeing quality to the end user.”
Methods of testing can range from a simple ‘Appearance’ assessment that evaluates a lubricant’s clarity, colour, texture, and smell in minutes, to a more complex, temperature-dependent analysis, which can take up to three days.
Two years into his role as Lab Chemist, it’s this comprehensive level of investigation as well as product development that has surpassed Thomas Roycroft’s hopes of what his role would entail. “I wanted to diversify, enhance, and develop the skills I had gained so far,” he explains. Thomas has combined on-the job learning with training offered by the company in partnership with the United Kingdom Lubricants Association (UKLA).
He continues: “The depth of processes required from start to finish when we’re formulating our products has surpassed my expectations. Certain products have a vast number of raw materials that need to go in for the oil to meet the performance demands that it will endure in its lifetime.
“This, therefore, requires an extensive test suite: from boiling point checks to running a viscosity check at -40°C and seeing how it fares against corrosion, the list goes on. Only then, once everything has been given the OK, can we ship out to customers knowing that it’s going to exceed requirements, and excel in the application that it is going to be required to go in.”
Behind the oil
With three decades of experience at Morris Lubricants, Andy Litchfield has been integral to building and maintaining the company’s reputation for producing quality oil. A fundamental part of this, he believes, must be attributed to using high quality base oils and additives.
“If you are formulating something, you need to have a very good understanding of what is available to make that product, depending on what properties you want it to have,” says Andy, who notes the launch and growth of water soluble metalworks lubricants as a career highlight. Another bench mark of the company’s success, he feels, is the strong relationship built with leading base oil suppliers.
He adds: “The quality goes back to the very start in terms of the raw materials that we buy. We work closely with respected and globally recognised base oil and additive providers to develop the correct formulations for our products. So, our products can be trusted to be fully supported by testing and validations.”