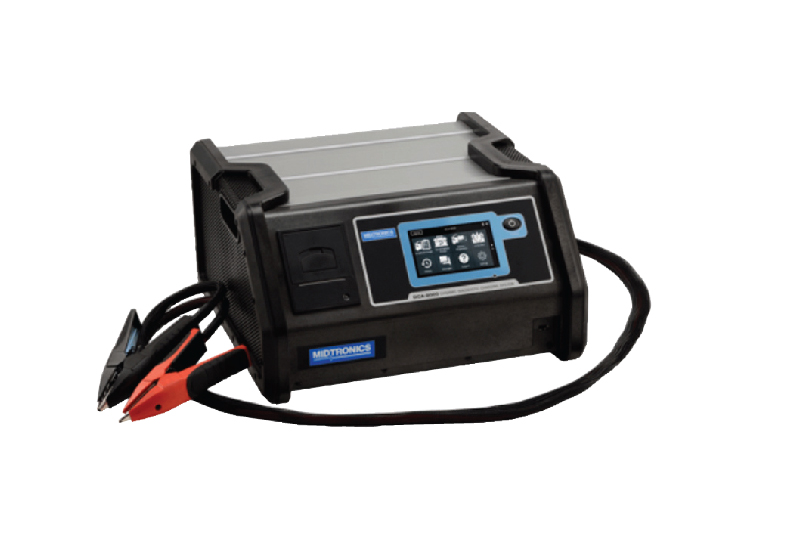
Ken Clark, Managing Director at Rotronics, highlights two examples where the company has been able to find the best method for tackling mounting battery problems and costs.
Case study 1
The first case study is from the emergency service sector. The Rotronics team works closely with a two-site workshop in the South of England, which is responsible for over 1,000 vehicles.
The problem
The original query to Rotronics came about because of recurring faults and issues with testers from another supplier.
None of the test results were accurate or credible. Repeated defects kept emerging, and the testers only monitored the starting capacity.
The load capacity result is vital to understand and that was not being recorded, and the considerable parasitic drains present were not being taken into account. So, the technicians were faced with misdiagnosis and repeated defects – and rising costs.
The solution
Rotronics had to do a lot of listening and analysing of complex issues; emergency service vehicles have to be 100% reliable and the stakes are high. They usually have constant parasitic drains with multifaceted requirements. The Rotronics team worked through a series of trials with a variety of combined options from its portfolio of professional testing and charging technology.
The trials helped deliver an excellent outcome. Two DCA8000s with 20 professional lithium chargers have now been set up within the two workshops. The equipment came with a tailor-made Rotronics battery management programme and the back-up of a full service and repair option, with ongoing support when needed.
The customer was absolutely delighted and reported back a 25% reduction in their battery-related defects and associated costs since working with Rotronics. They can now pinpoint issues and fix problems. The workshop manager said the new equipment was a bit like having a crystal ball. He also reported that the workshop mindset has totally changed, and the sceptics are now advocates of the new technology because of the great changes in reliability and budget savings.
Case study 2
The second case study follows Rotronics’ work with a national distribution, express freight, logistics, warehousing, and haulage expert during 2021.
The problem
The fleet is made up of 600 vehicles and potential expansion plans meant that the management team wanted to invest in a comprehensive battery management programme to reduce the current level of defects, roadside breakdowns, and rising costs – and also increase distribution productivity.
The team walked Rotronics through their requirements, and Rotronics created a personalised battery management programme with the correct mix of products for the technicians. In initial trials, they enjoyed using the Midtronics EXP1000FHD tester because it identifies any battery faults ahead of them turning into costly non-starts.
Warranty claims were also causing issues due to limited battery data being available. Sometimes these defects were occurring on fresh new vehicles, so it was problematic to be able to confirm warranty claims without back-up data.
The engineering team sought advice regarding technology to use with AGM and Regular Flooded batteries, due to breakdowns triggered by in-vehicle electronics and driver facilities.
The solution
Rotronics worked with the management team and technicians to develop a programme based on using the Midtronics EXP1000FHD tester and the Midtronics PRO50/2 charger, coupled with a year’s subscription to ROBIS, the remote battery management platform.
The EXP1000FHD allows technicians to record individual VIN and fleet numbers. This helps the management team identify which vehicles have been tested in the workshop. ROBIS is fully compatibility with the EXP1000FHD, so that technicians can access live fleet battery data which is excellent when dealing with warranty claims. The PRO 50/2 charger offers combined charge acceptance and battery conditioning for both 12V and 24V fleet batteries.
Rotronics’ customer now has visible battery data, and the personalised battery management programme also includes training options and ongoing backup support when required, to ensure the best return on investment for the fleet.