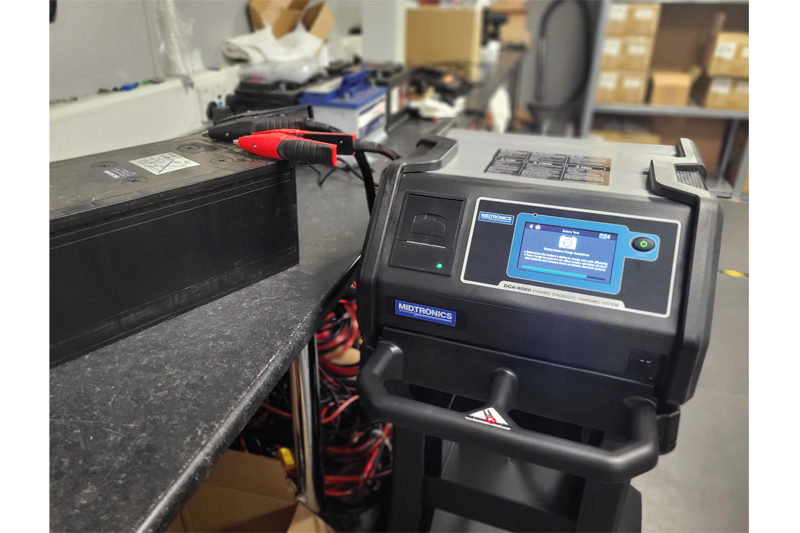
Rotronics’s managing director, Ken Clark, helps readers with the best options of looking after battery technology and keeping the workshop budget in good shape.
We feel pretty confident that most people will be familiar with the concept of keeping waterproofs waterproof. Just chucking them in the washing machine without any technical cleaners and wash-in waterproofing will eventually mean that one day you will be soaked through.
There are some clear differences, but not looking after your vehicle batteries has real similarities and can land you in the same predicament. This is about using the right technology and taking care of it, therefore saving money. By looking at some data pulled out of our battery information dashboard ROBIS, we can get a clear picture of battery health across independent hauliers, commercial fleets, OE commercial, PSV, emergency vehicle and emergency vehicles.
Based on data from 25,500 vehicles which have been well looked after, tested and charged last summer and winter, one can readily assess the cost savings to be made in workshops, just through improved battery management.
From test results, we know that last winter 26,500 batteries needed charging: that is just over 13,000 vehicles. It can be shown by the data that those 13,000 vehicles would have broken down if left unattended and the maths on that number is shocking. Each breakdown costs roughly £350, give or take, so that means that an unnecessary spend of £4.5 million was averted, simply through correct battery management.
Shocking fact
The summer months are always kinder to battery technology but, even so, 22,900 batteries needed charging, which is 11,450 vehicles, a spend of over £4 million. Again, something which can be averted because of improved battery management.
Where the spend gets more shocking is when we look at our data for batteries that needed to be replaced in the same periods. Even when batteries are well looked after, they may get to a replacement stage.
Last winter, the average replace decision from tests was around 19% of all tests and that equates to 15,000 batteries. In summer there is an improvement of a couple of percent, but it still comes to 9,800 batteries. The average price of a battery is £180, give or take again, and so that means an additional new battery spend of £2.7 million in the winter and £1.8 million in the summer. If workshops in the data group had not been testing and charging, they would have had to shoulder those new battery costs in addition to the breakdown costs.
Shocking fact
This might seem alarmist, but a look at the data from ROBIS to see how many of the 25,500 batteries tested were in good condition, did not need charging and the vehicles had no breakdown risk is enlightening. Last winter, it was only 45% and in summer it was only 50%. That is leaving a large margin for error, breakdown and expense because of battery failure.
These data clearly show that battery management processes, testing and charging according to the test result are all essential to keeping a workshop’s battery spend as tightly managed as possible. That is something that all readers will be feeling very keenly in the current climate.