A cost-effective way to fix axle threads
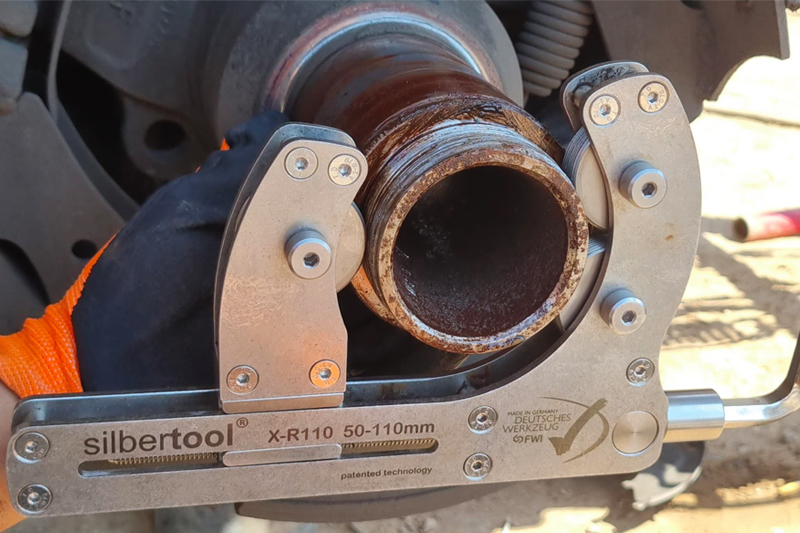
First spotted at Road Transport Expo (RTX) 2024, Thread Saver gives workshops a quick and cost-effective method of repairing damaged axle threads and wheel studs. According to UK distributor Premier Pits, repairs can take as little as 31 seconds. CVW reports.
The first UK sale of Thread Saver has already shown its potential for cutting costs and saving time. A bus operator with a severely damaged axle thread was able to complete the repair on the same day it received the tool, saving at least £10,000 by avoiding the replacement of costly components, according to the distributor.
Manufactured in Germany and Estonia by Silbertool Solutions, Thread Saver reforms rather than cuts damaged threads. Traditional thread repair tools, such as thread cutting dies, remove material during the process, weakening the thread. Thread Saver takes the opposite approach. Instead it restores the thread without any material loss, maintaining its strength and load capacity after the repair. The result – a reliable repair without compromising the integrity of the thread.
Repair time savings
Workshops using Thread Saver can expect to see time savings during repairs. According to Premier Pits, the tool can repair a damaged axle thread in as little as 31 seconds, with no need to strip down the hub or send axles away for repair, minimising vehicle downtime and maximising productivity.
The repair process itself is straightforward but requires precision. First, the damaged thread is inspected to determine the extent of the damage. The operator then selects the appropriate Thread Saver tool size based on the thread specifications and cleans the area to remove any debris or contaminants. Once the tool is aligned with the existing thread, a lubricant is applied to ease handling, and the thread is gently reformed using the tool. Afterward, a gauge is used to verify that the repaired thread meets required specifications.
According to tests conducted by the Material Testing Institute Hannover (MPA), threads repaired using Thread Saver can withstand the same static and dynamic loads as new, undamaged threads. The repaired threads even demonstrated a higher fatigue endurance limit, ensuring that they remain robust over time.
The tool is versatile too. It comes in kit form, complete with the Thread Saver XR-120 for axles (with 1.5mm and 1.5mm LH, 2.0mm and 12 TPI roller sets), and the X-Nut XL for use on wheel studs. As a result, the distributor says, it is suitable for commercial vehicles, public service vehicles (PSVs), and even rail applications. The tool is also rugged enough to perform reliably in demanding workshop environments. It is made from premium-grade stainless steel that is vacuum-hardened and tempered to 58 HRC, a process that ensures low wear and high ductility. It is also light and compact, making it easy to store and carry.
Premier Pits suggests that the cost savings achieved through Thread Saver extend far beyond the initial purchase price. By repairing instead of replacing expensive components, workshops can save both time and money. In the case of the bus operator who made the first UK purchase, Premier Pits points to the repair’s rapid completion and the substantial financial benefit as evidence that Thread Saver can provide a quick return on investment.
The manufacturer behind Thread Saver has a reputation for producing high-quality equipment not only for the automotive industry but also for specialised, safety-critical situations. One project involved creating a 300 kg tool for a one-time use, repairing threads on pipes leading into the incinerator of a nuclear reactor. This tool had to be operated from behind a lead curtain, five meters above the ground, through 2mm gaps.
Premier offer
Another project required a tool for fixing hundreds of threads on bridge foundations over a highway, with each thread passing micro-crack detection tests, and another for rolling new threads on studs of a water retention dam, allowing for tension tests.
The manufacturer’s UK partner, Spalding-based Premier Pits has served industries such as HGV, bus, coach, rail, and defence for more than 40 years and is best known for designing, manufacturing, and installing a wide range of prefabricated vehicle pits, under-chassis wash systems, and ATF packages and buildings.