Are cordless power tools the way forward?
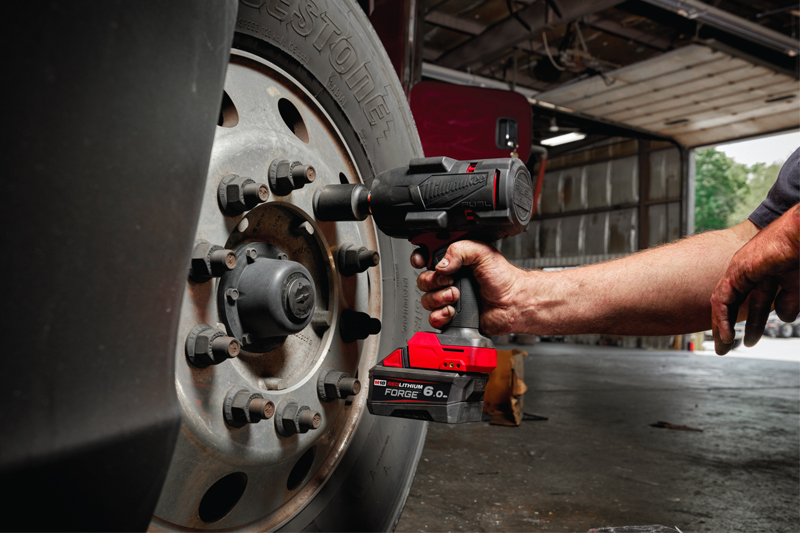
Are cordless power tools changing the way workshops operate? CVW spoke to Milwaukee Tools to find out what is influencing the way garages are working.
The wide use of pneumatic air tools within workshops began in the early 20th century. When air powered tools were first released, they were considered the solution to have for increased job efficiency whilst reducing strain on mechanics. However, as the world entered the 21st century a new era of power tools began. The range of lithium-ion powered tools has now exceeded the number of corded and pneumatic power tools within the market, offering countless workshop solutions. Many lithium-ion solutions can outperform corded and air tools providing a more portable, ergonomic and efficient way of working. For example, Milwaukee’s latest battery technology FORGE has taken cordless power tools a step further, providing the most powerful, fastest charging and longest life batteries.
Milwaukee and Midland Air Tools have collaborated to provide an insight into the changing dynamic of commercial vehicle workshops across the UK, highlighting the benefits of switching to cordless solutions within the industry. As its name suggests, Midland Air Tools was built through its focus on the distribution of pneumatic power tools. Whilst they still offer an extensive range of air powered solutions, the introduction of Milwaukee’s power tool range has supported the internal operations of commercial vehicle companies such as Scania. Previously, Scania utilised air tools in its workshops before making the switch to Milwaukee’s cordless solutions.
There were several key factors influencing Scania toward cordless power tools. Firstly, pneumatic air tools rely on compressors to provide the air pressure needed, compressors vary in size dependent on the size of the workshop and the number of tools being run off the system. They require installation, maintenance and have poor energy efficiency, which all generate additional running costs for a workshop.
Cordless power tools are simple to setup, low maintenance and are up to 95% more energy efficient than an air tool running off a compressor, approximately 30% of the air produced by compressors is lost between the air tank and the tool.
Aside from pneumatic air tools being inefficient to run, they also pose a trip hazard and restrict mobility around the workshop. Air lines, due to their design are the second most likely cause of a non-fatal accident in a workshop. Cordless power tools offer increased mobility, remove the risk of a trip hazard from an airline and can provide adequate power to carry out most commercial vehicle repairs.
HAVs or not
Furthermore, all commercial vehicle workshops should monitor and assess the risk of vibration white finger when using power tools to ensure that necessary measures are taken to protect employees. Vibration white finger is a symptom of hand arm vibration syndrome (HAVS) and over the last couple of years there has been a disturbing rise in HAVS cases in industries previously not considered risky, like the service sector and this includes the vehicle repair industry.
That is why workshops should include the use of a HAVS exposure equation to ensure a maximum trigger time is not exceeded by their technicians. Midland Air Tools conducts its own HAVS analysis on every tool it sells and has recently put Milwaukee’s ½in high torque impact wrench to the test against the average exposure of 10 pneumatic ½in impact wrenches.
Testing was carried out using both Milwaukee’s standard M18 RedLithium 5Ah battery and its new M18 RedLithium FORGE 6Ah battery. The results from the test highlighted that the new FORGE battery increased the permitted trigger time by 23 minutes against the same tool using an M18 5Ah battery and by 15 minutes in comparison to the average of 10 pneumatic ½in impact wrenches.
The results really speak for themselves, providing mechanics the opportunity to get more work done without putting themselves at risk in doing so.