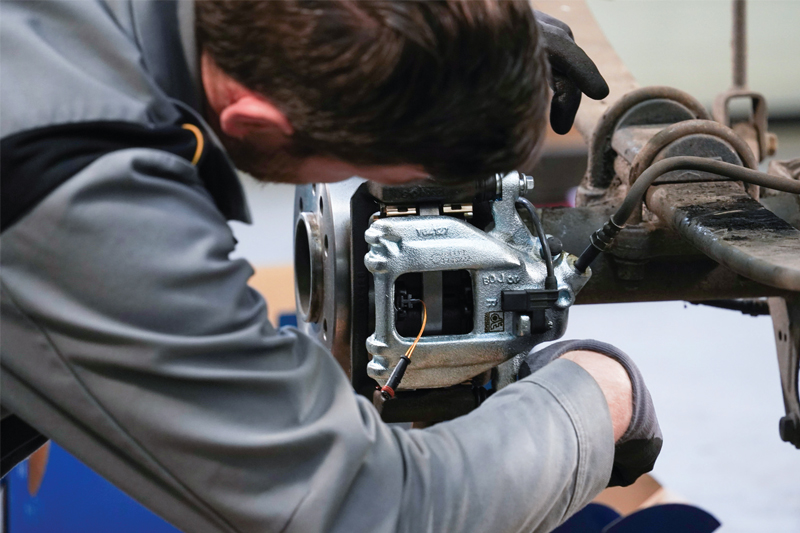
When you’re looking for answers, video has now become the go-to. CVW talks to Diesel Technic’s parts specialists, Lars and Kevin, whose YouTube videos have over 12,000 subscribers, about brake systems, identifying common error patterns and offering practical solutions.
‘Show’ is often better than ‘tell’ when it comes to problem solving, according to the Parts Specialists. “We always work through a live issue in our workshop videos, for example in the brakes systems video we are working on a transporter that is experiencing one-sided sluggishness on the right brake,” says Kevin.
When checking the service brake, Kevin quickly sees that the sleeves are damaged, and dismantles the brake caliper and brake pads, including the caliper carrier.
Lars runs through some of the common error patterns to look out for on brake pads, using examples to highlight key issues.
“Wear patterns and glazing on brake pads can indicate whether the pads are installed correctly or need adjustment. In the first example, the contact pattern was incorrect, and the disc has worn unevenly. As a result, the pads are also glazed due to thermal load, with a shiny appearance across the surface. The bluish discolouration and porous surface also indicate extreme thermal stress. The consequences here are stiff brakes or other defects in the brake system,” he explains.
“Checking is absolutely essential,” cautions Lars. “It becomes dangerous when the brake pads no longer completely bear on the friction surface of the brake disc, as this reduces the braking effect.”
In another example, he points to a pad, once again glazed due to thermal load, where the brake disc is smooth at the top on the edge. “If the pad only rests at this point or the brake disc only grinds here, it can begin to squeak.”
Most vehicles are equipped with wear sensors (simple contact wear sensors or digitalised detection systems) that indicate the wear of the brake pads. This allows a defect, or ‘normal’ wear of the components to be detected in time. “For any pads that you want to replace but you want to keep the old brake disc, if the gauge hasn’t been reached yet, lightly chamfer the edges, this way you prevent noise,” he says.
Thermal overload is also reflected in drum brake linings through glazing, discolouration, cracking or even the parts being torn apart. Lars shows an example with extreme glazing which as a result means the braking effect cannot be achieved. He points to the bluish discolouration and crack formation, all of which indicates a thermal overload. “In this case the trailer control valve was defective. Here a compressed air system caused this, which resulted in the thermal overloading of the brake pads, and therefore the drum is now also defective. It’s really important to make sure that the pressures are right.”
In the next step, the two Parts Specialists show what should be considered when changing the brake pads for the parking brake. “Among other things, greasing the parts should never be neglected. However, care should be taken that the lubricant does not come into contact with the braking surfaces,” says Kevin. The new brake caliper is installed together with the repair kit, including guide rails, screws, sleeves and grease to ensure that the items run smoothly. Key tips from the Parts Specialists:
- Cleanliness is the be-all and end-all, because impurities that get into the brake system or the brake fluid can damage the sleeves or seals internally. The consequences would be repeated failure of the brake caliper.
- To find out the wear limit of the brake discs, use a caliper gauge. It is important to use a special brake disc caliper with measuring tips to obtain a meaningful result.
On the brake disc that Kevin is working on, the wear limit is 14mm, which is written on the disc but is now difficult to see. They replace the disc not only because at 14.3mm it is almost on the wear limit but also because it has a slight edge. Kevin notes that it’s also possible for brake discs to be cracked. “If they are completely cracked or cracked through to the cooling channel for larger brake discs, they must be replaced. Sometimes they may only have a small crack, in which case please check the manufacturer’s information as to when they need replacing.”
After the complete renewal of the brake system, Lars takes the transporter out for a short but slow spin around the yard to loop the handbrake in. More detailed information on the individual work steps involved in finding common brake errors, can be found on the company’s YouTube channel.