How to reduce tyre-related operating costs
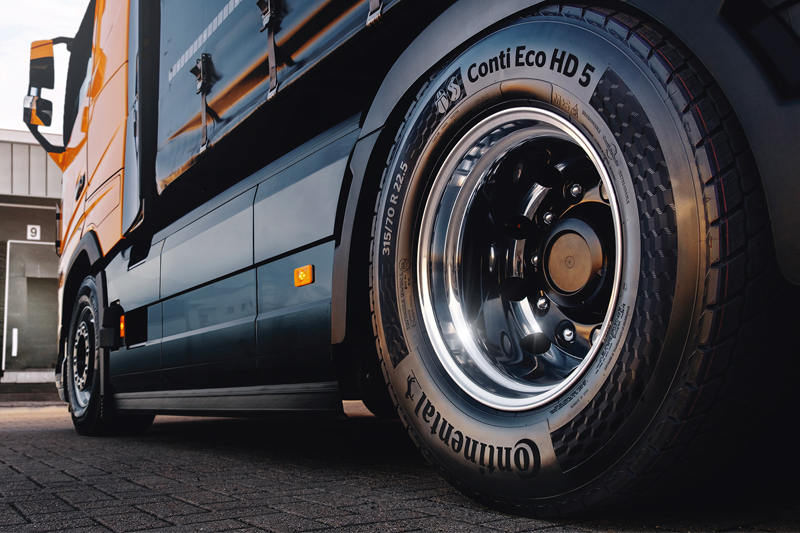
CVW dusted off its passport and travelled to Hannover to attend the launch of Continental’s new Conti Eco Gen 5 tyre line up. Here’s what we learnt.
You only need to visit Continental’s HQ in Hannover to understand just how seriously the company takes its environmental responsibility. Home to 2,400 employees, the six-building campus is powered, heated and cooled by natural resources – solar and geothermal. It even collects rainwater for re-use, charges the electric cars and bikes of its staff from solar panels and ensures that the office environment is both pleasant and sustainable through the use of materials such as wood, stone and natural fibres.
This adherence to sustainable principles and commitment to detail is just as evident in the launch of its new range of tyres for the freight industry – the new Conti Eco Gen 5. Three years in the development, thousands of hours on the test bed and on the open road and an approach informed by research carried out by the Boston Consulting Group, and you can tell that no stone was left unturned in the search for the optimum tyre solution.
One key finding was that while tyres might only account for 2% of operating costs, they actually influence around 50% of operating budgets, so every enhancement made can have a significant beneficial impact helping what Continental termed the ‘Lowest Overall Driving Cost’ (LODC).
Challenges met
So, what did Continental do? For a start it optimised rolling resistance and higher mileage capability – classically conflicting goals in the world of tyre development. “In the past, if a tyre ran particularly smoothly and therefore needed less drive energy, that might come at the expense of robustness and durability,” points out Hinnerk Kaiser, who is responsible for the development of truck and bus tyres at Continental. Now the Continental boffins concentrated on mileage-neutral measures to improve rolling resistance across all components – in the construction of the casing, the treads and the design of the overall contour and tread. The treads, with their two-layer construction (cap base) and innovative compounds, enable a high mileage and considerable robustness while also optimising rolling resistance. The road contact compound (cap) allowed the developers to focus on mileage and robustness.
At the steer axle, a thicker under-tread reduces rolling resistance – but it also enables tread compounds with a focus on extending mileage. At the drive axle, the optimised shoulder design with innovative sipe form in the tread shoulder area plays a key role in promoting even tyre wear – which also has a positive effect on mileage. In the casing, several compound components and a new bead geometry are tailored to optimise rolling resistance. These measures combine to produce an up to 12% improvement in rolling resistance and an up to 10% increase in mileage over the two predecessor products.
The optimised rolling resistance and high mileage of the new Conti Eco tyres have a positive effect on their environmental footprint. “If our product increases the fuel efficiency of a truck and lasts longer, the result is lower CO2 emissions,” adds Kaiser. Choosing the right tyres is therefore becoming even more important, not least given the emissions-based toll charges for fleet operators in the EU. “Replacing the outgoing EcoRegional HS 3+/ HD 3+ with the new Conti Eco HS 5/ HD 5 tyres across a fleet of 100 vehicles – which cover around 80,000 km per year in regional use – can save up to €69,000 and 120 tonnes of CO2.”
Retreads are go
Added to which, the new tyres also make a convincing impression with their excellent grip, allow heavy goods vehicles to display safe and secure handling – even in fluctuating weather conditions – and offer outstanding traction throughout their lifespans. Customers can also ask for them to be delivered directly from the factory with latest-generation sensors. This allows the Conti Eco Gen 5 to drive the progress of fleet digitalisation and – in conjunction with the ContiConnect 2.0 tyre management solution – enables remote monitoring in real time and predictive service planning. This helps to substantially reduce tyre-related operating costs, as do the retreading solutions from Continental. “We designed the casings of the new Conti Eco from the outset to make them ideally suited to retreading.
The new tyre line also contributes in this way to greater cost efficiency and sustainability in the transport sector,” finishes Kaiser. A retreaded tyre consists up to 70% of material from the old tyre and costs up to 40% less than a new tyre, while offering equal mileage and safety. The new Conti Eco tyres will be available in numerous sizes, starting with the following:
- 315/70 R 22.5 Conti Eco HS 5
- 315/80 R 22.5 Conti Eco HS 5
- 385/55 R 22.5 Conti Eco HS 5
- 385/65 R 22.5 Conti Eco HS 5
- 315/70 R 22.5 Conti Eco HD 5
- 315/80 R 22.5 Conti Eco HD 5