BorgWarner explores turbocharger efficiency
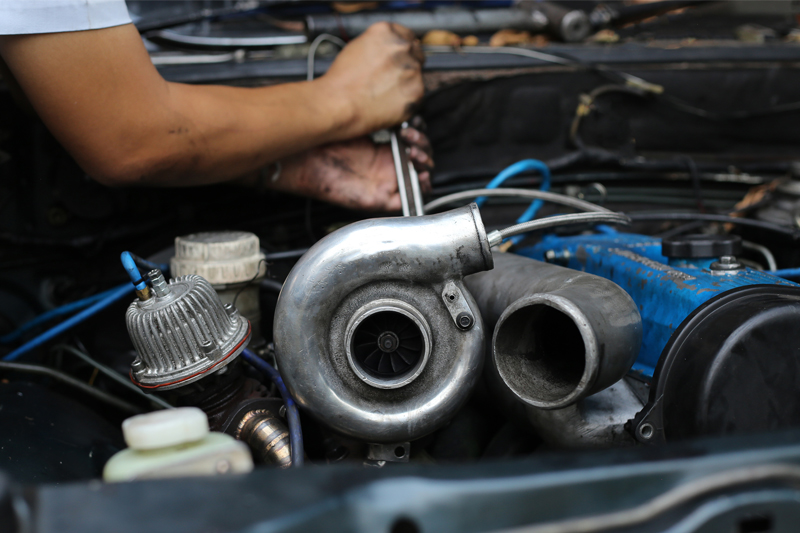
Michael Boe, vice president and general manager Global Aftermarket, BorgWarner Emissions, Thermal & Turbo Systems discusses how to maximise the life of a turbocharger, and identifies some checks to carry out before assuming turbo failure.
Although it is feasible for a turbocharger to last the life of the engine on which it’s installed, fleets and independent operators are now keeping their vehicles so much longer that the need for turbo replacement will inevitably become more commonplace as the vehicle population ages. However, it is possible to maximise the life of this component with diligent attention to routine vehicle maintenance.

Lubrication
The first prerequisite is that the vehicle/engine manufacturer’s service schedule is followed, with particular attention to the engine’s lubrication system; more than 40% of turbo failures are oil related, two of the major causes being dirty oil or oil starvation. The rotating parts of the turbocharger are precisely balanced and float on a thin film of engine oil; considering the tight clearances between them and the high speeds experienced at the bearing surfaces, any oil contamination or starvation can soon cause failure. Therefore, oil and filter change intervals must not be exceeded, the quality and specifications of the oil need to be adhered to, and the correct functioning of the oil circulation system must be ensured.
Air and fuel
A further cause of early turbo demise is damage to the compressor wheel caused by a foreign body entering the intake; this can be avoided by ensuring that the air filter system is working effectively and is serviced in clean working conditions. Correct calibration and functioning of the fuel injection system is also vital, as a fault here can lead to elevated exhaust temperatures, which in turn can damage the turbine wheel or crack the turbocharger housing.
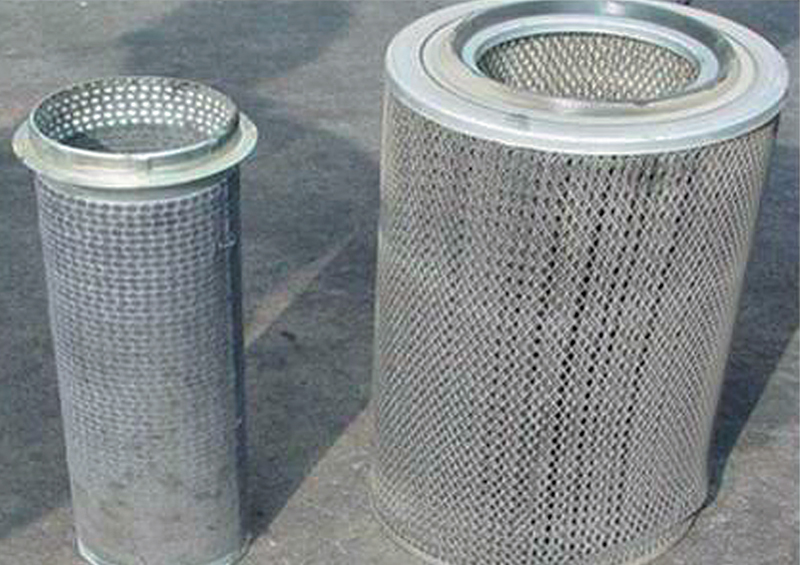
Diagnosing smoke
Excessive smoke at the exhaust pipe is often assumed to be an indication that the turbocharger has failed, resulting in many being replaced when in fact there is another cause within the engine or one of its ancillary systems that should be investigated first. In particular, the air filter, exhaust system, breather system and fuel system should be confirmed as working properly, as problems in any of these can cause similar symptoms to turbo failure.
Either black or blue smoke may be observed. Certain faults are common to both: on the intake side a clogged air filter, or a dirty compressor or intercooler; on the exhaust side a blockage in the exhaust system or leakage upstream of the turbine; or in the engine itself, valve guides, piston rings, or cylinder bores/liners may be worn, giving rise to increased blow by of combustion gases. If no issues are found here, it could indicate damage to the turbocharger bearings.
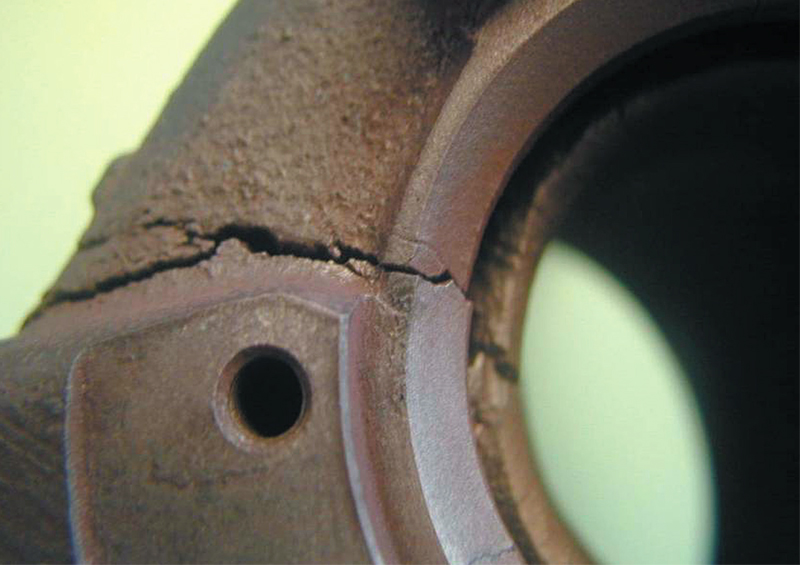
Additionally, black smoke may point to a combustion problem; fuel delivery or defective or poorly adjusted fuel injection leading to over- or under-fuelling, or an air leak at the inlet manifold or plenum chamber due to it being cracked or poorly sealed – so check gasket condition and torque settings of the fasteners. Joints in the intake system suction and pressure pipework should also be checked for air leaks. Another possibility is that the wastegate is not closing properly, in which case a lack of engine power will most likely also be evident. If all of these items prove satisfactory, it’s time to check for damage to the turbocharger’s compressor or turbine wheels, or to the turbine housing.
Finally, blue smoke can also be caused by a blocked or leaking crankcase ventilation system, or by a problem with the oil drain tube, which could be kinked, clogged or leaking. If this is not the case, look for coke and sludge deposits in the centre housing of the turbocharger.
Unexpected noises
Several of the checks for the cause of exhaust smoke are also applicable to finding the source of an unusual noise. Any of the parts that transfer intake air or exhaust gases and are subject to pressure or vacuum can give rise to whistling noises if they leak. Likely to be more serious is a high-pitched squeal – particularly under boost – which may be due to bent or damaged compressor wheel or turbine blades making contact with the housing.
As can be seen from the brief outline above, there are many possible causes of exhaust smoke or unusual noises that must be ruled out before condemning the turbocharger itself. BorgWarner offers an online turbo diagnosis tool to assist.
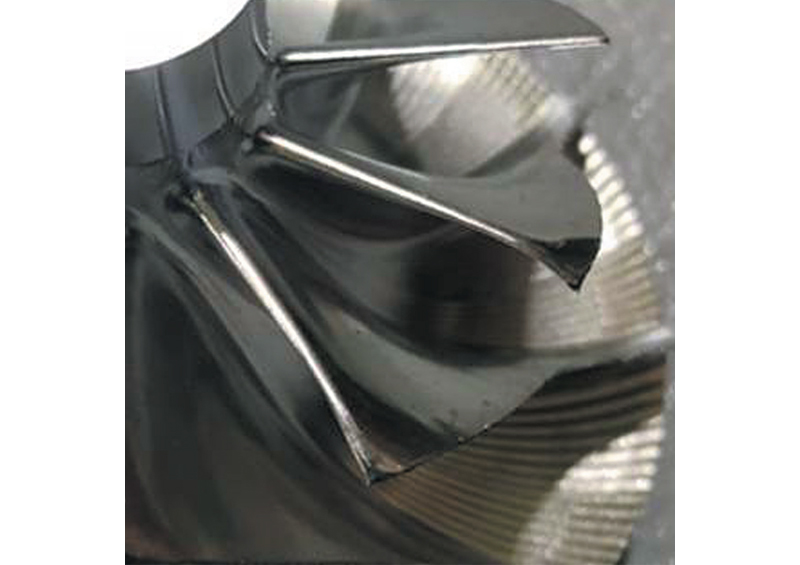
Original or reman?
When a genuine problem with the turbocharger indicates that a replacement is needed, there are two choices – new or remanufactured. Reman parts are popular for the older fleet, as they represent a cost-efficient solution relative to a vehicle’s declining value. Apart from the cost benefit for the customer, they also carry the appeal of improved sustainability. But regardless of whether the turbocharger is new or remanufactured, always opt for a part from a recognised OE turbo manufacturer brand such as BorgWarner, and source from an authorised dealer to avoid the possibility of buying a counterfeit item.