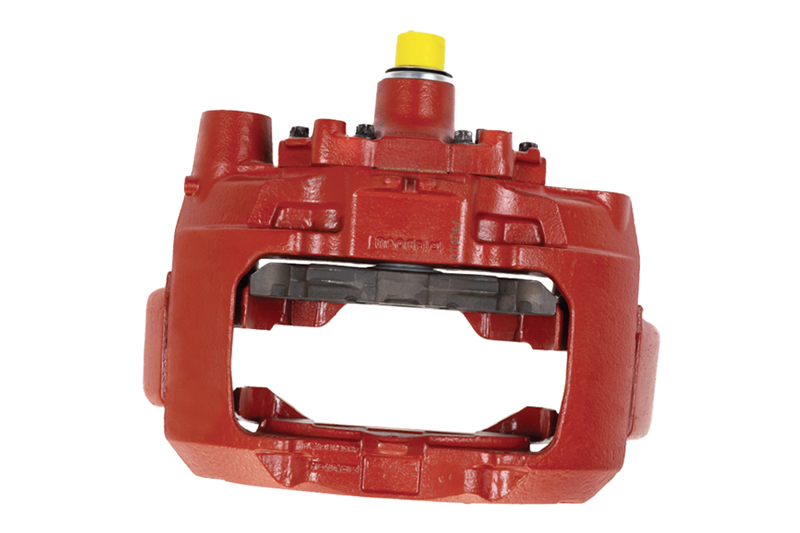
Keith Sedgley, Roadlink Managing Director, discusses the importance of the remanufacturing process and why it’s an environmentally-friendly alternative.
Commercial vehicle brake specialist Roadlink International has long been a fervent believer in the remanufacturing process, reflected in the company’s ongoing investment in reman and its commitment to helping reduce the company’s carbon footprint. Roadlink remanufacturing promotes quality whilst also offering a competitively priced, environmentally-friendly alternative.
Remanufacturing in the UK currently contributes massively to the UK economy and is expected to grow dramatically thanks to further investment. It is not only good for the environment through the reduction of CO2 emissions but cuts down on raw material and energy consumption.
As one of the UK’s leading suppliers of braking products for commercial vehicles and buses, Roadlink currently offers a complete range of new and remanufactured braking components including brake shoes and brake calipers.
Remanufacturing promotes the reengineering of a product to the same or indeed better than the OE equivalent. It’s clear to see why the quality of such parts, much more competitively priced, attracts so much attention and use.
Brake shoes
Roadlink brake shoes are not only more environmentally friendly, with all worn linings reprocessed for use within the construction industry, but also offer a cost-effective solution to the CV aftermarket without compromising on quality.
Remanufacturing is a vitally important, growing aspect of this industry, not only does it help drive energy conservation and the reduction of raw materials usage, but also the elimination of landfill space.
As part of its continued investment in brake shoe relining, Roadlink provides a ‘Brake Assured’ Production Process, with the company being the first in the UK to achieve the coveted status, providing a guarantee that brake shoes are fully remanufactured to the highest product quality and safety standards possible, with OE-quality brake linings and rivets.
Roadlink’s state-of-the-art brake shoe reline operation is supported by ISO9001 approved production and ISO14001 environmental accreditation, with every shoe platform checked and linished.
Its 15-stage production process for relining brake shoes is something Roadlink strictly adheres to, which involves rollers being checked where applicable and shoe platforms treated with an anti-corrosion long lasting water-based paint, unique to Roadlink.
An inspection is undertaken after each stage and shoes come supplied with a full warranty and product liability insurance.
Having established its position for nearly 40 years in the CV brake shoe market, Roadlink has one of the largest ranges in Europe and all brake shoes come complete with OE brake linings to suit all types of truck, trailer and PCV applications.
Roadlink’s advice: If you are considering buying remanufactured brake shoes make sure you choose you choose a company who offer only ‘brake assured’ OE-quality friction materials such as Textar, DON or Roadlink. After all, safety is critical.
Brake calipers
Through continued investment in its remanufacturing facility, Roadlink currently offers a complete range of new and remanufactured braking solutions.
Roadlink remanufactured calipers are fully-tested and produced to the highest standards thanks to its extensive state-of-the- art on site production facility and distribution operation, which are certified to the latest ISO9001:2015 quality and ISO14001:2015 environmental standards.
Produced to the highest standards, Roadlink brake calipers represent the widest range and the best quality available in today’s market.
Roadlink remanufactured calipers are engineered onsite in dedicated production facilities to perform at least as well as the original. All worn and safety critical components are replaced throughout the remanufacturing process and multi point quality checks are completed from start to finish. With dedicated buildings for strip and reassembly the processes are always kept separate.
Every unit is fully stripped in, and all components and bodies are inspected for wear, damage or corrosion – with worn, damaged or suspect parts replaced with original specification components.
All internal and fastener threads are cleaned, inspected and rectified if required, and all seals and protective covers are automatically replaced. Each unit is fully tested following reassembly, and securely packed in Roadlink-branded cartons.
Each unit is fully traceable down to component level and given a final check over by a member of our team before being boxed for sale. Roadlink remanufactured calipers not only offer the highest product quality but provide the CV Aftermarket with excellent value for money.