The problems that arise from vibration
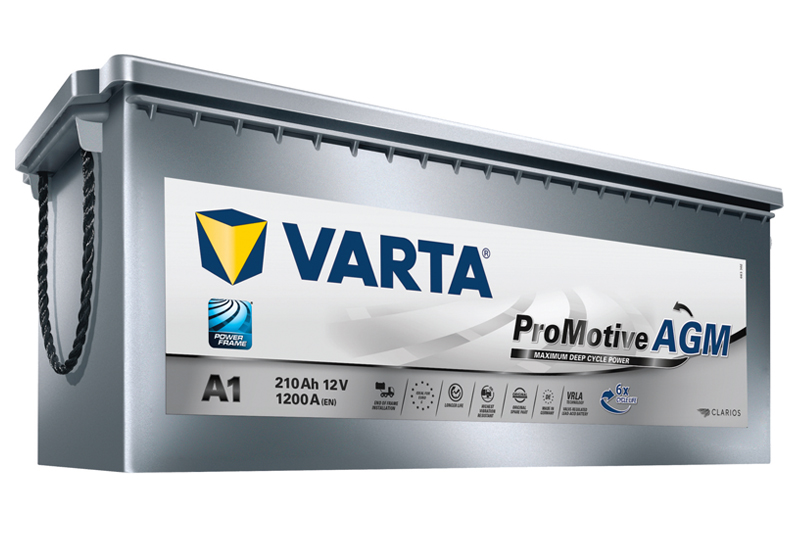
Shaken and stirred? Ecobat Battery looks at the consequences of vibration related battery failures and offers a few remedies to the problem.
Dealing with the problems that arise from vibration, which is generated by almost every moving object, is an ongoing issue for the trucks that ply their trade on the highways of the UK and across the continent, particularly in respect to the batteries they rely on to provide the electrical energy that these vehicles need to operate.
This existing issue was made worse with the introduction of AdBlue (diesel exhaust fluid) systems used in Euro 5/6 compliant engines, when most commercial vehicle (CV) manufacturers chose to relocate the position of the battery trays to the rear of the chassis, where vibrations tend to be more prevalent and which can contribute towards premature battery failure, particularly to traditional SLI (starter, lights and ignition) batteries, which are already vulnerable to vibration.
The most obvious solution to this particular issue is to fit a battery that is better suited to resist the vibration so prevalent at the rear of a truck’s chassis, and among the options is to choose AGM (absorbent glass matt) or EFB (enhanced flooded battery) alternatives, as both designs have considerably greater resistance to vibrations, as well as being able to withstand a larger number of charge/discharge/charge cycles than SLI batteries.
Despite the fact that both AGM and EFB batteries are more expensive than their SLI cousins when initially purchased, they are considerably more cost effective when factors such as the total cost of ownership (TCO) and potential vehicle breakdowns are considered as well.
It is widely accepted that the greatest loss to an operator is to have a vehicle stranded by the side of the road, because the considerable reputational damage is magnified by potential late delivery charges and the obvious recovery costs, and relying on SLI batteries will only increase these risks.
To reduce these risks, we’ve long championed the principle of upgrading a specified original equipment SLI battery when it needs replacing – with options such as the ODYSSEY AGM or VARTA ProMotive AGM or, utilising another technology, the Exide Endurance+PRO GEL.
For the most energy demanding requirements, the ODYSSEY AGM reduces the risk of a call out to what might only be a flat battery by 60% and safeguards the ability for starting, compared to a conventional SLI battery. These batteries also overcome the electrolyte and vibration issues of SLI batteries by incorporating AGM separators, meaning the acid is fully absorbed, so it cannot sink, and as the plates all sit on a rubber base and are top welded together with hot rubber melt, they have vibration resistance built in. Allied with an inherent fastcharging capability even from 80% of discharge, with this option, battery related breakdowns become a very rare occurrence and as they deliver twice the power and three times the life of SLI batteries, they are typically lasting for four years plus, which significantly reduces the TCO.
For similarly high demand situations, the efficient technology incorporated into the VARTA ProMotive AGM provides the solution for trucks with a heavy reliance on numerous power consuming functions, including parking cooler/heaters, without wearing out and causing downtime. It has been developed in collaboration with the leading CV manufacturers to support innovations that will be standard equipment in the future.
Gel batteries differ from other battery types because instead of being in liquid form, the electrolyte is fixed in a gel, which leads to unmatchable cyclic (charge/discharge/charge) life. Furthermore, as Exide Technologies is the inventor of gel technology, its Endurance+PRO GEL battery is not only highly robust, but also offers the best-in-class deep cycle properties that allow an unmatched safe depth of discharge of 90%.
Largely due to the requirement for operators to adhere to environmental legislation, the electrical demands put on batteries are further stretched by initiatives such as ultra low emissions zones, which often require vehicles to operate without their engine running, meaning the battery is the sole source of power. As a result, over time, the battery’s state of charge can suffer, as the vehicle’s charging system is rarely in a position to fully recharge the batteries.
There is, however, a solution to this situation, which is also a best practice principle that will further contribute to the vehicle’s overall reliability, increase the lifespan of its batteries and further reduce the TCO, and that is to actively charge the batteries when the vehicle is not in service.
Although Ecobat Battery is fully committed to this practice, it is also keen to highlight a practical matter that must be taken onboard, and that’s the charge voltage required by these various battery types. While SLI, as well as gel, batteries require between 13.8 and 14.4 volts, it must be noted that AGM batteries require a charge voltage of between 14.6 to 14.8. This may not sound like a big difference, but if AGM batteries don’t get this higher voltage when they are in a discharged state, they won’t get charged properly, which could reduce their service life.
Naturally, we have a solution for this issue, and this comes in the form of the Victron IP65 Blue smart charger, which is capable of charging all battery types for both 12 and 24v systems and will allow fleet operators to keep the batteries in their vehicles in the best possible condition and reduce the likelihood of battery related breakdowns.