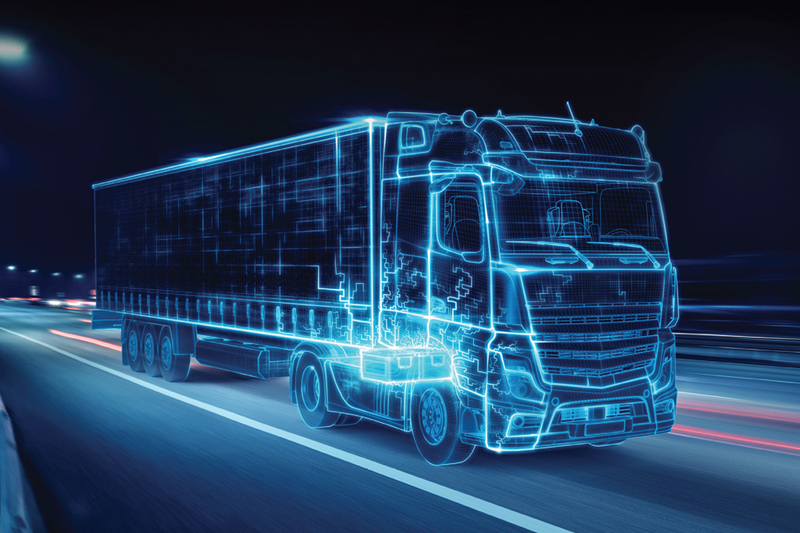
As the colder weather and cost-of-living crisis in the UK continues, Andy Cook, technical trainer at VARTA, urges managers and workshops not to cut corners when it comes to battery maintenance and replacements.
Due to soaring energy costs and rising inflation, there is a temptation for some to take the ‘easy route’ and skip maintenance or install standard flooded batteries in their highly equipped vehicles. At first glance, it might seem like the cheaper option, but it will end up costing more in the long run.
With record numbers of shoppers expected to turn to the web looking for discount deals as household budgets are squeezed and purchasing groceries online and getting them delivered to the front door continues to become the norm for many families, the demands put on Britain’s transportation fleets and delivery vehicles are increasing.
It has been reported that this has put a strain on many courier companies, with extended delivery times being advised due to demand outstripping capacity. This has impacted many fleets, as additional vehicles have been put into action and additional routes are being used, but often at the cost of vehicles maintenance schedules not being adhered to.
What this means is, many delivery vehicles have not had the care and maintenance they would usually do, and jobs like carrying out regular battery maintenance and testing have been skipped. Battery maintenance is something that should be routinely carried out, particularly on fleet vehicles that might not have been serviced for some time. This ensures the vehicle’s batteries are in good working order and won’t let them down whilst on the road. Breaking down due to battery failure can often be costly as recovery of larger trucks is expensive and also penalties can be incurred for late delivery.
Do away with convention
These days, conventional batteries have a hard time keeping up with the large amount of energy-draining electrical devices that modern trucks are equipped with. Trucks are on the road for longer which means more overnight stays in the cabin – with increased expectations regarding comfort. Refrigerators, microwaves, coffee machines and entertainment electronics lead to deeply discharged batteries after the rest periods.
On top of that, there is an increasing number of legislations to be met. Advanced fuel saving technologies like coasting/sailing and passive boost are on the rise in order to reduce CO2 emissions and overall consumption. Together with AdBlue® tanks taking up additional space, this often makes an end of frame installation close to the rear axle necessary, subjecting the battery to increased vibrations. High robustness and vibration resistance are therefore required.
The latest, leading Absorbent Glass Mat (AGM) batteries have passed both lab and road tests and fulfil four key requirements to be labelled an original spare part:
- Cold cranking power
- Cycling performance and deep discharge capabilities
- Vibration resistance
- Charge acceptance
The eponymous glass mat fleece absorbs the battery acid and increases cycle stability. This prevents loss of capacity due to acid stratification, the main cause of battery failure in modern trucks. The advantage: the battery has a lifetime expectancy of two years and longer. To reach a comparable lifetime with a regular battery would result in its drop of capacity down to 20%. Due to the design of leading proprietary AGM batteries, however, up to 80% of the specified capacity can be utilised without significantly compromising cycle lifetime.
It provides the ideal power supply for vehicles equipped with comfort and safety functions and advanced fuel-saving features such as coasting/sailing. AdBlue tanks and larger fuel tanks are displacing batteries towards the rear end of commercial vehicles. Even when situated in this location AGM batteries are able to withstand increased vibrations, preventing premature failure.
Total cost of ownership
Fleet managers of today expect reliability from their vehicles as well as from their choice of spare parts. They put their trust in leading technologies and brands to ensure minimum risk of downtime and constant optimisation of their fleet’s total costs of ownership (TCO). If you already have a lot of well-equipped trucks, it’s worth upgrading them to an AGM battery. It gives drivers and fleet operators additional security against battery failures, reduces overall operating costs and ensures satisfied customers for the truck manufacturers. Leading AGM batteries are absolutely future-proof and still have a lot of free capacity available for additional energy consumers.
This is particularly important given the current economic conditions as fleet managers will want to take advantage of cost savings. While the initial outlay of AGM technology is higher than purchasing a standard flooded battery, when you consider they last four to six times longer, depending on style of driving/journey, in the long run they are the more cost-effective option. Especially when you consider when used in conjunction with a thorough maintenance schedule you should avoid costly breakdowns.