Why check the auxiliary belt regularly?
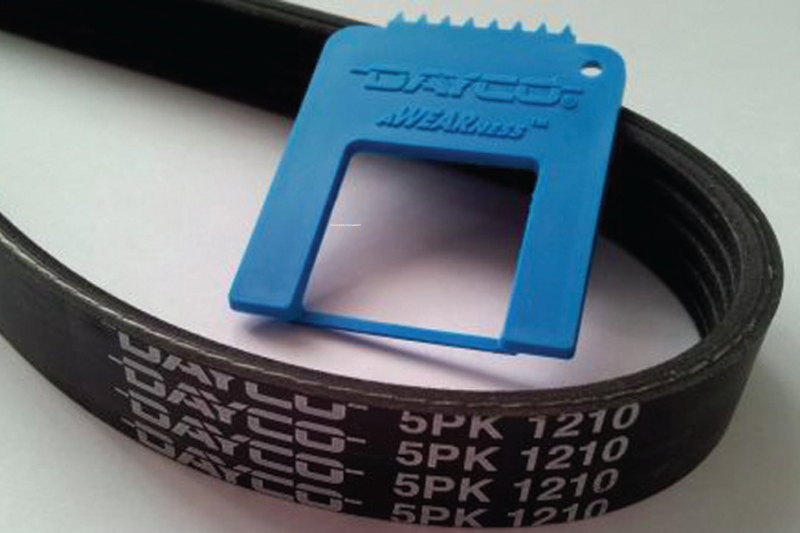
Checking the auxiliary drive system reduces downtime, says Ann-Marie Dean of Dayco.
Although often overlooked, the harsh reality is that should an auxiliary belt fitted to a commercial vehicle fail, alongside the need to replace the affected parts, the vehicle’s time off the road, must also be factored into the potential cost of ignoring the condition of the belt. This could easily exceed £500 per day for those fleets employed on a daily national delivery contract, as well as having the additional costs to shell out for roadside repair or recovery.
As a result, Dayco is encouraging CV operators and workshops to take a broader view and check the auxiliary system every time a vehicle enters their premises, particularly as according to ADAC data, across Europe, auxiliary belt failure is the main reason for engine related breakdowns.
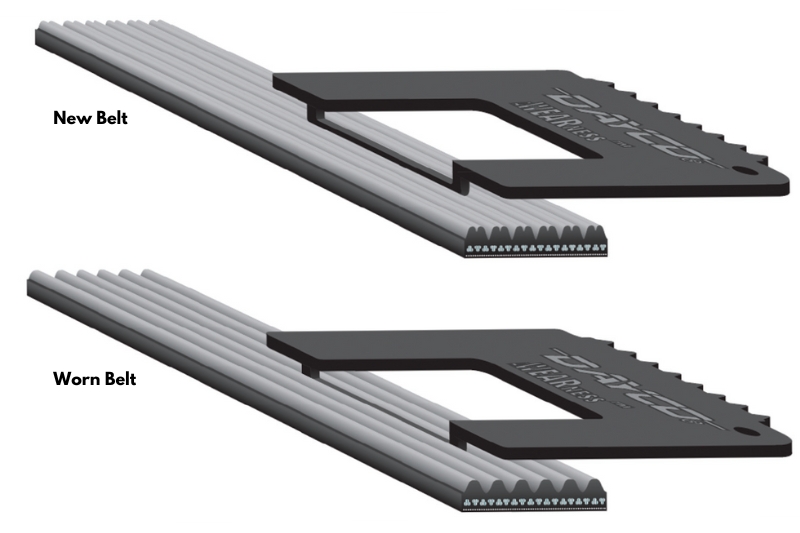
Revenue driver
Dayco estimates that there are 100,000 systems that require maintenance annually, so applying our ‘check & change’ principal every time a vehicle enters the workshop will help operators mitigate these financial costs. In addition, as CVs generally have more than one belt system, it also provides business opportunities for workshops.
As both a reliability measure and safety precaution for the operator, and a potential profit opportunity for the workshop, checking the auxiliary drive system of every vehicle that comes in is a smart move, especially as the UK market is estimated to be worth £7.5 million on belts alone!
Although the check doesn’t take long, as a typical EPDM belt wears gradually like the tread wear of a tyre, technicians need a simple tool to help them.
Our aWEARness gauge provides three ways to check whether the belt needs to be replaced or is okay to be reinstalled. The two most relevant to an EPDM belt are the wear indicator bar, which highlights material loss (fig A) and the profile indicator, which reveals whether the belt retains its correct form (fig B,C). Both reflect the level of wear and if the belt fails either check, it must be replaced.
Although we suggest checking the belt every time the vehicle comes in for inspection, as a benchmark we recommend that for off-highway vehicles the belt should be checked every 28,000 miles and changed every 56,000 miles. When it comes to trucks and buses this can be extended to 37,000 miles and 74,000 miles respectively for vehicle operation in an urban environment, and to 74,000 and 148,000 for those covering long distances.
Tension
Wear on the belt could also indicate wear to the other components in the auxiliary drive system, which is why technicians also need to thoroughly assess the condition of these associated parts. Particular attention should be paid to the tensioner because the wrong tension on the belt can exacerbate wear and contribute to the potential failure of the drive system.
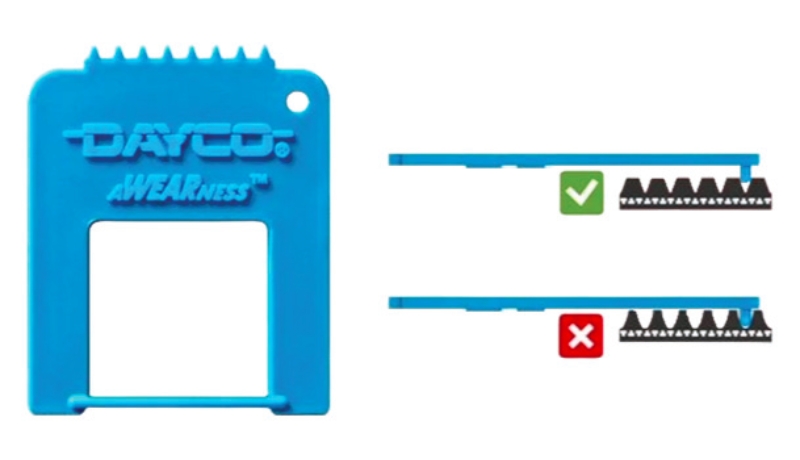
In order for technicians to carry out the best possible job and fleet managers to maximise the reliability of their vehicles, the auxiliary drive system should be considered as a single entity. So, instead of looking at the belt and drive components separately and potentially changing individual items, technicians should replace the complete system, which allows them to provide a thorough repair solution.
Helpfully, Dayco provides a ‘one stop shop’ for auxiliary system maintenance and replacement because, as well as its OE designed belts, it also supplies tensioners and pulleys, which means that technicians have the assurance that they are installing fully compatible parts. With water pumps also included in its aftermarket offering, its auxiliary drive support is complete.
As a full system supplier to many vehicle manufacturers globally, we only produce vehicle specific references. As a result, it doesn’t compromise the aftermarket with a ‘one size fits all’ policy, and this means that technicians are able to install a like for like, OE replacement.
When it comes to the aftermarket, independents can rest assured that our OE pedigree flows through to our aftermarket offering, because the company’s manufacturing facilities, engineering processes and finished products are identical for both its OE and aftermarket supply channels.
Both, therefore, reflect the latest technology, so technicians can be assured of the correct installation when it comes to the components, which means the fitting time is minimised, alignment of the auxiliary system optimised and the correct function of the components in the auxiliary drive system is secured.
Our commitment to the independent sector also means we are constantly bringing relevant additions into the range to ensure that CV workshops have the parts they need, when they need them.