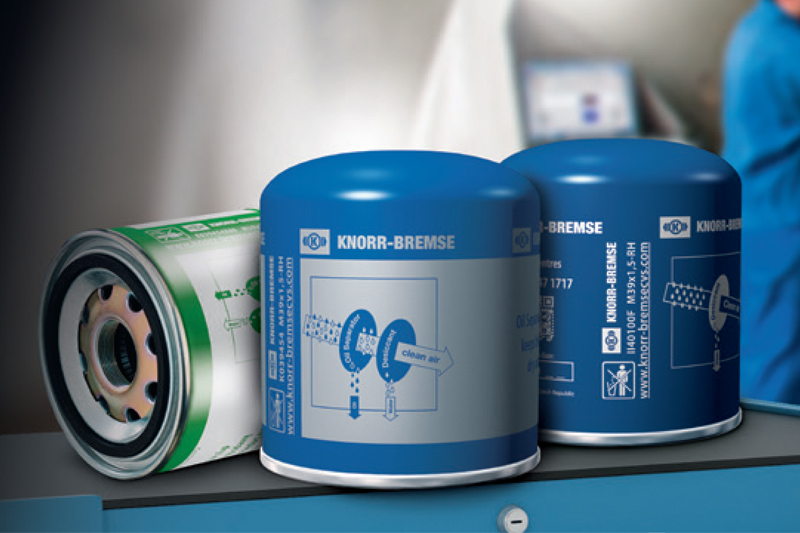
Oil contamination in compressed air systems affects braking performance and increases downtime. Here, Knorr-Bremse explains how Oil Separator Cartridge technology solves the problem.
Compressed air systems require clean and dry air to work efficiently and safely. Knorr-Bremse has developed air drying systems for all the leading OEMS and has manufactured over 30 million air dryer cartridges, so understands what the requirements are and what happens to them in service.
The problem
Oil contamination of the air system is inevitable over time. It comes from the oil used to lubricate and cool the piston, crankshaft and bearings. As a piston goes up and down, the piston rings cling onto the oil to help lubricate the bore(s) and some of it inevitably gets through the rings.
Older and badly remanufactured compressors will pass far more oil than new OE units. In conventional air dryer cartridge systems, after around 120,000 km and assuming an oil carry-over rate of 1g/h), it’s possible that up to two litres of oil may have been transferred from the compressor. Over time, these oil residues in the desiccant can substantially diminish the drying performance of air dryer cartridges – and consequently the performance of the brake system.
This can lead to the brake system becoming contaminated, reducing the life span of the cartridge, impairing its performance and leading to the failure of downstream components, and thus additional downtime and repair costs.
The solution
In contrast to many alternative air dryer products, the Knorr-Bremse Oil Separator Cartridge (OSC) removes oil and dust particles from the compressed air before it comes into contact with the desiccant. The sophisticated aerosol and oil filtration technology incorporated in the OSC prevents even the smallest particles from entering the desiccant, so that the drying performance remains constant over a long period of time. Service intervals are up to 36 months for normal air consumption, and 24 months for high-demand applications.
Technology comparison
On the left is the Knorr-Bremse cartridge with aerosol and oil filtration system. On the right of this are examples of alternative air dryer cartridges. In the top example, the oil filter is downstream of the desiccant, while in the lower cartridge, the oil filter is upstream of the desiccant.
Cost-effective reman option
Operators looking for a value-based maintenance solution can also benefit from OSC cartridge technology. A remanufactured OSC is available in Knorr- Bremse’s EconX remanufactured product range, providing a cost-effective solution that does not compromise on filtration quality. Service intervals are 24 months for normal air consumption applications and 18 months for high-demand.
Cartridges undergo a robust process for controlled disassembly and cleaning and any reused components are checked to ensure they meet design specification of a new component. Crucially, end of line testing is equal to the testing standard for a new cartridge.
Remanufactured components also require significantly reduced material input compared to a new cartridge, together with the amount of energy used and the associated CO2 emissions.