Hartridge investigates the reason there is more than one filter in the exhaust system and what their differences are.
It has been said that necessity is the mother of invention, and modern compression ignition engines are such an example of remarkable engineering. In order to achieve their necessary power and performance every facet of each component is in finely tuned balance. Further development arose thanks to the necessity to comply with emissions standards, and several techniques to cater to this requirement emerged.
DOC, DPF and SCR Filters
The diesel exhaust aftertreatment system has arisen to solve one problem; the difficult task of removing harmful particulate matter from diesel engine emissions. Untreated emissions from a diesel engine contains a cocktail of harmful chemicals and particulate matter, however today’s system can reduce this down to harmless substances, oxygen, and water. The exhaust after treatment devices that are applied to vehicles are Diesel Oxidation Catalysts (DOC), Diesel Particulate Filters (DPF) and Selective Catalytic Reduction (SCR) catalysts. Using a combination of physical mechanisms and chemical reactions these systems can, under the right conditions, achieve near complete removal of particulates and harmful gases. There are many variances between these systems but the biggest differences between DOC, DPF and SCR filters lies in their individual purposes.
Regeneration
The DOC is the first device in the after treatment system. It is a flow-through filter that contains precious metals to start the oxidation of hydrocarbons, carbon monoxide and unburned fuel and oil. Both the DOC and the DPF are honeycomb ceramic filters. However, unlike the DOC, the DPF is a wall-flow filter that traps any remaining soot that the DOC couldn’t oxidize. The soot remains in the DPF until it is regenerated either passively or actively.
Passive regeneration occurs when the vehicle’s normal operating temperatures and the DPF will oxidise the particulates anywhere between 275-360 ̊C. Active regeneration is instigated when sensors detect an excessive build-up of particulates within the DPF. Raw fuel is injected into the exhaust stream to trigger temperatures over 600 ̊C, which are required to oxidise the build-up of soot.
Back pressure usually returns to normal after the soot is gone, however, don’t forget about the ash! Ash builds up inside the DPF and does not burn or oxidize like soot and will remain until removed. Ash is made of minerals, metals and other trace elements from the breakdown of lubricants, additives and engine wear. Ash builds up at a much slower rate than soot but if ignored will eventually cause increased back pressure, fuel consumption and sometimes DPF failure. As ash builds inside the DPF the number of active regenerations increase causing poor fuel economy, extreme high temperatures, and more constant back pressure that can be detrimental to the turbo charger. The longer the ash is left inside the DPF, the greater the chance of it hardening into a plug which closes off a portion of the filter. A vehicle operator will be the first to notice the shorter intervals between regenerations, which is the first clue to ash build up and the need to remove the DPF for cleaning. This can also be observed by data logging the regen cycles in the workshop with diagnostic equipment. When the DPF is removed for cleaning it is always a good practice to also remove the DOC, and clean it as well if necessary.
The last component in the after treatment system is a flow through SCR catalyst which introduces Diesel Emissions Fluid (DEF) to the process. This fluid contributes to the further break down of nitrogen oxides that pass through to the SCR filter. Typically the SCR filter doesn’t need maintenance except in rare events where a component related to the DEF fluid fails.
Core Contents
At the heart of these components is an ultra-fine filter, which captures microscopic particulates. A DOC can contain more precious metals than a DPF and metals such as platinum bonds with the oxygen molecules in hydrocarbons. A DPF’s core can be made of a few different materials but the most common are cordierite composites. An SCR catalyst has valuable filter contents in the form of ceramic materials and precious metals.
All these filters contain a specific recipe of metals selected for their role in the chemical reactions necessary to effectively clean the emissions. In addition, they are manufactured with materials to resist the higher temperatures of an active regeneration cycle. Unfortunately, the core materials of these filters have made them the target of thefts, especially on vehicles with high ground clearance like people carriers, vans, and trucks.
Maintenance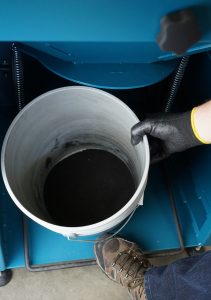
Although these filters differ in their purpose on the vehicle, they all share the need for maintenance and servicing
because the filters can still get congested in their own ways. If blockage builds up it can cause irreparable damage to the exhaust system resulting in massive repair costs, unscheduled vehicle down time, and particulate matter entering the environment. The DPF and DOC filters are suitable for pneumatic and thermal cleaning; conversely, because the SCR is a closed unit it is not suitable for the pneumatic cleaning. It can still get blocked by hardened DEF and if this happens it is not usually serviceable.
A balancing act
These filters and catalysts are just as sensitive as the rest of the engine and in equally delicate balance with each other. They are in harmony with the engine’s operation but also respond to how the car is driven. Therefore it is logical to need a DPF cleaning solution that can flex and adapt to the fact that a workshop will be working with filters in a range of serviceable conditions. The Hartridge DPF300 Master Series is a set of four machines that work in harmony to tailor the clean and thermal treatment to exactly what that DPF requires.